RD-E: 5400 Cut Methodology
The target of the cut methodology is to study one area of the model by applying the deformation of the full model to a smaller model.
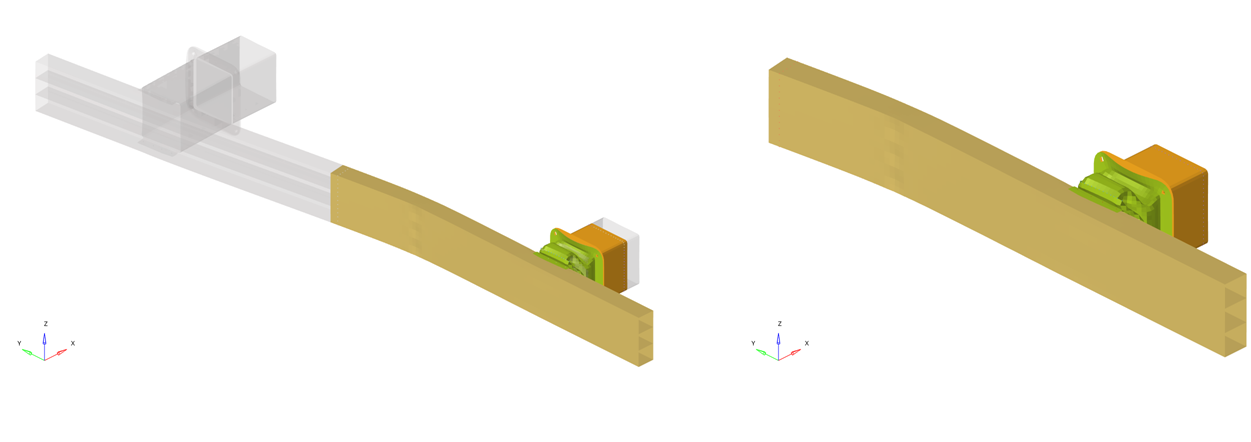
Figure 1. Full Model and Sub-Model
Options and Keywords Used
- Section (/SECT)
- Elastic material (/MAT/LAW1 (ELAST))
- Elasto-plastic material (/MAT/LAW36 (PLAS_TAB))
- Rigid wall (/RWALL)
- Self-impacting contact (/INTER/TYPE7)
- Tied contact (/INTER/TYPE2)
- Rigid body (/RBODY)
- Advanced Mass Scaling (/AMS)
- Boundary conditions (/BCS)
Input Files
- Frame Modified
- <install_directory>/hwsolvers/demos/radioss/example/54_cut_model/*
Model Description
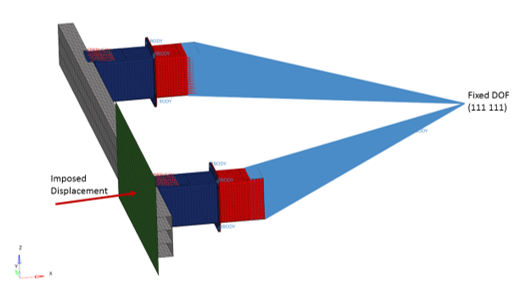
Figure 2. Problem Description
Units: mm, ms, kg, N, GPa
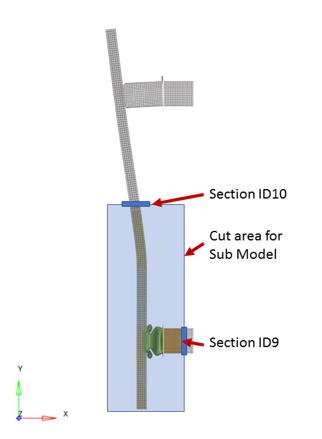
Figure 3. Full Model Results with Suggested Cut Location to Create the Sub-Model
In order to focus on the crash box area just behind rigid plate, the sub-model (blue highlighted area in Figure 3) is cut from the full model. To have the same behavior as the sub-model and the full model, the force and displacement on the boundary of the selected are needed. Using /SECT, it is possible to save and read section force or displacement.
The node groups and element groups in the section should be the same in the full model and sub-model to ensure consistency between the forces. It is also possible to use HyperMesh to create the /SECT in the full model and create the sub-model by deleting elements from the full model.
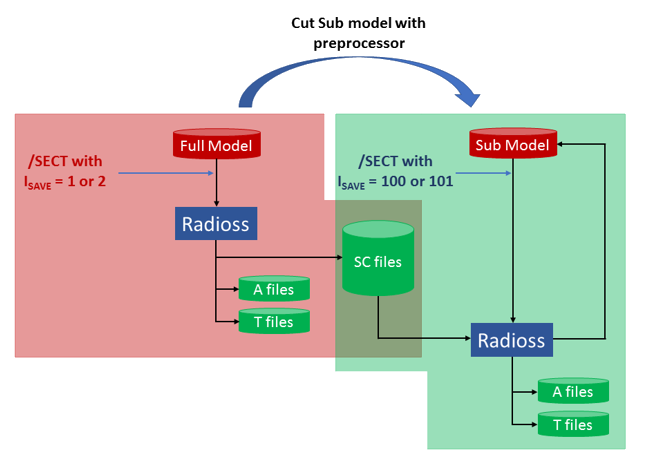
Figure 4. Cut Methodology in Radioss
Results
Full Model | Sub-Model | Ratio Sub-Model / Full Model |
|
---|---|---|---|
CPU | 1 | 1 | |
Number of Elements | 16722 | 9730 | 58.19% |
Time step [ms] | 0.1500E-02 | 0.1500E-02 | 1 |
Elapsed time [s] | 498.62 | 272.16 | 54.58% |
The computation time is reduced because there are fewer elements and contacts in the simulation.
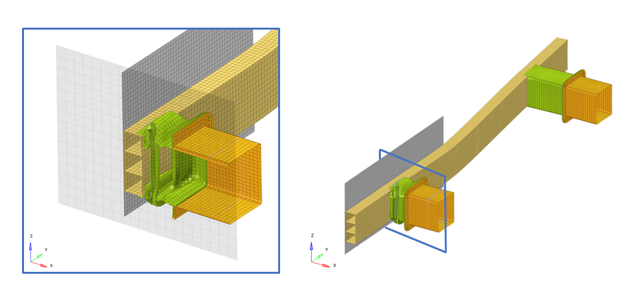
Figure 5. Deformation Overlay of the Full Model and Sub-Model
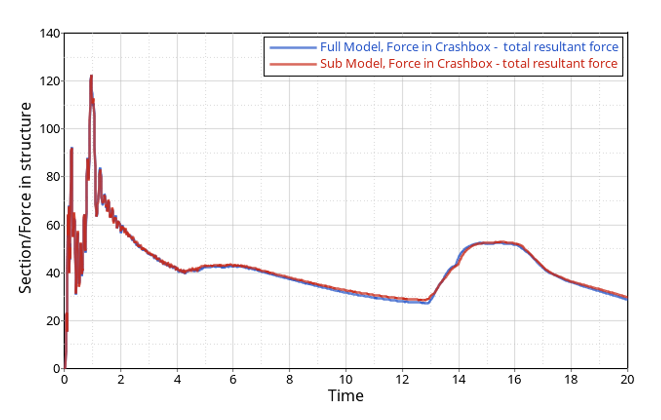
The cross-section force in the crush box is very similar between the two simulations. If the sub-model results are very different than the full model, more section output results can be saved in the SC file by reducing the /SECT . Alternatively, the location of the sections could be modified to include a larger area from the full model that influence the deformation of the sub-model.
Conclusion
The cut methodology allows you to reduce the computation time by running smaller models. Its main limitation lies from the fact that the interactions between the selected parts in the cut model and the unselected parts must be small enough so that the behavior of the selected parts is not significantly affected by unselected parts. It is important to compare the section force (or moment) between the full model and sub-model to make sure they are similar.
In industrial applications, such as a car simulation with crash dummies, it is advised to keep only the dummy and its direct environment as sub-model. Then about 90% of the CPU cost could be saved compared to the full car model. In low speed impacts or the beginning of impact with high speed, it is advised to keep only the deformed area as sub-model. Then about 30% of the CPU cost could be saved compared to the full car model.