RD-E: 1802 Square Membrane Elastic
This example concerns the in-plane traction-comparison problem of an embedded plate subjected to two concentrated loads, as shown in Figure 2.
This example illustrates the role of the different shell element formulations with regard to the mesh.
Options and Keywords Used
- Q4 shells
- T3 shells
- Hourglass and mesh
- Boundary conditions (/BCS)
The boundary conditions are such that the three nodes of a single side and the two middle ones are blocked, whereas the others are free with respect to the Y axis.
- Concentrated loads (/CLOAD)Two concentrated loads are applied on the corner points on opposing sides. They increase over time, as defined by the following function:
F(t) 0 10 10 t 0 200 400
Figure 1. Boundary Conditions and Loads
Input Files
- 4Q4
- <install_directory>/hwsolvers/demos/radioss/example/18_Square_plate/Membrane_elastic/4Q4/.../TRACTION*
- 8T3
- <install_directory>/hwsolvers/demos/radioss/example/18_Square_plate/Membrane_elastic/8T3/.../TRACTION*
- 8T3 inv
- <install_directory>/hwsolvers/demos/radioss/example/18_Square_plate/Membrane_elastic/8T3_inv/.../TRACTION*
- 2Q4-4T3
- <install_directory>/hwsolvers/demos/radioss/example/18_Square_plate/Membrane_elastic/2Q4-4T3/.../TRACTION*
Model Description
Units: mm, ms, g, N, MPa
- Material Properties
- Initial density
- 7.8x10-3
- Young's modulus
- 210000
- Poisson ratio
- 0.3
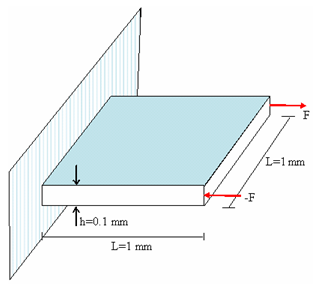
Figure 2. Geometry of the Problem
Model Method
- Mesh 1
- Two quadrilateral shells and four triangular shells (2Q4-4T3)
- Mesh 2
- Four quadrilateral shells (4Q4)
- Mesh 3
- Eight triangular shells (8T3)
- Mesh 4
- Eight triangular shells (8T3 inverse)
- QBAT formulation (Ishell =12)
- QEPH formulation (Ishell =24)
- Belytshcko & Tsay formulation (Ishell =1 or 3, hourglass control TYPE1, TYPE3)
- C0 and DKT18 formulations
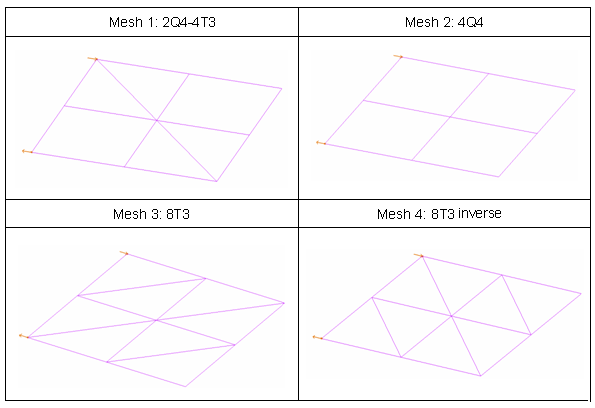
Figure 3. Square Plate Meshes
Results
Curves and Animations
- the use of different element formulations for each mesh
- the different types of mesh for a given element formulation
- absorbed energy (internal and hourglass)
- vertical displacement of the node under the loading point
The following diagrams summarize the results obtained.
Energy Curves / Comparison for Element Formulations
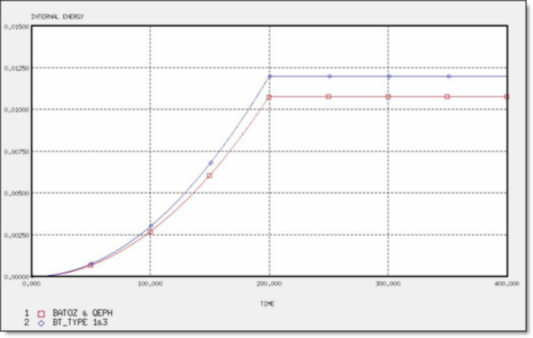
Figure 4. Internal Energy for 2 x Q4 and 4 x T3 Elements
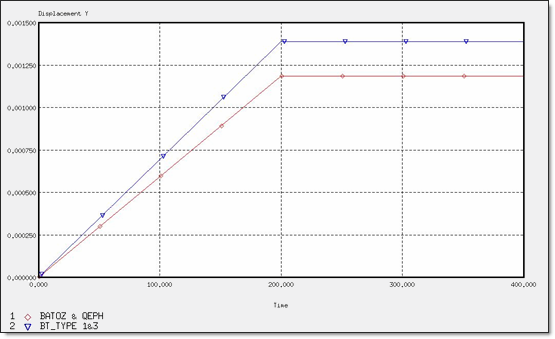
Figure 5. Y Displacement for 2 x Q4 and 4 x T3 Elements
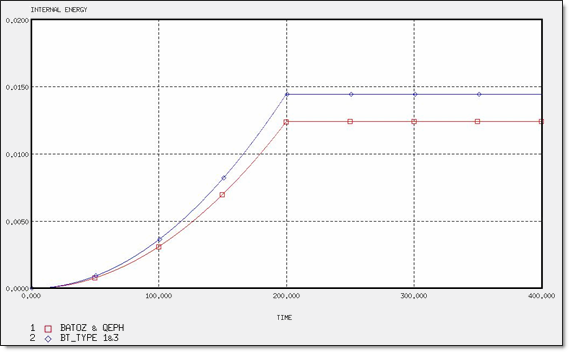
Figure 6. Internal Energy for 4 x Q4 Elements
Energy Curves / Comparison for Mesh Definitions
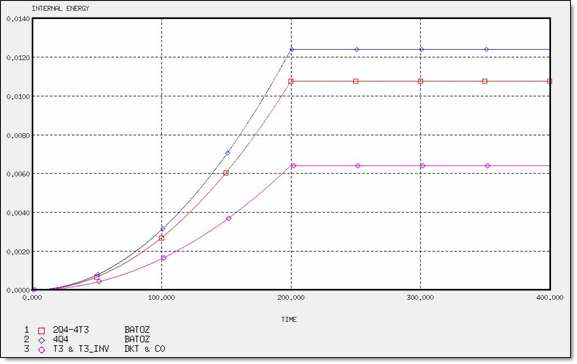
Figure 7. Internal Energy for Different Meshes
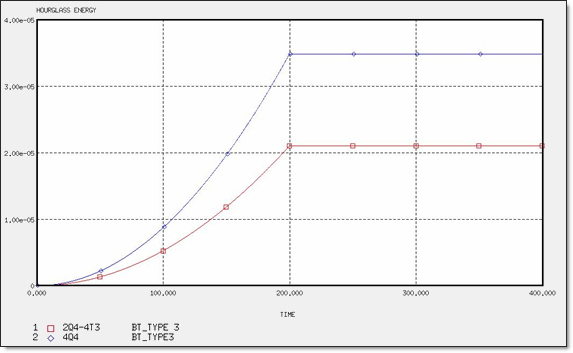
Figure 8. Hourglass Energy for Different Meshes
Elastic Plate | 2Q4-4T3 | 4Q4 | 8T3 | 8T3_INV | ||||||
---|---|---|---|---|---|---|---|---|---|---|
QEPH | BT_TYPE 1 and 3 | BATOZ | QEPH | BT_TYPE 1 and 3 | BATOZ | DKT | CO | DKT | CO | |
IEmax | 1.07 x 10-2 | 1.19 x 10-2 | 1.07 x 10-2 | 1.24 x 10-2 | 1.44 x 10-2 | 1.24 x 10-2 | 6.42 x 10-3 | 6.42 x 10-3 | 6.42 x 10-3 | 6.42 x 10-3 |
HEmax | --- | 2.10 x 10-5 | -- | -- | 3.49 x 10-6 | -- | -- | -- | -- | -- |
Dymax | 1.18 x 10-3 (Traction) | 1.38 x 10-3 (Traction) | 1.18 x 10-3 (Traction) | 1.24 x 10-3 | 1.44 x 10-3 | 1.24 x 10-3 | 6.42 x 10-3 | 6.42 x 10-3 | 6.42 x 10-3 | 6.42 x 10-3 |
Conclusion
In the case of elastic flat plate modeling, when the loading is in-plane, the shell elements are reduced to become a membrane if the loads applied do not cause buckling.
- The quadrilateral shell elements QEPH and QBAT have the same in-plane behavior.
- The different types of hourglass formulations in the BT shell elements lead to the same results, as there is no out-of-plane deformation and the material is supposed to be elastic.
- The three in-plane behaviors of the DKT18 and T3C0 Radioss triangles are exactly the same, as both of the elements are used for the same membrane formulation.
- The triangles are stiffer than the quadrilateral elements and do not provide good results, especially when the mesh is coarse.
Refer to the Radioss Theory Manual for more details.