RD-E: 4802 Solid and Spring Spotweld in Crash Box
The purpose of this example is to introduce solid element modeling for spotweld connection.
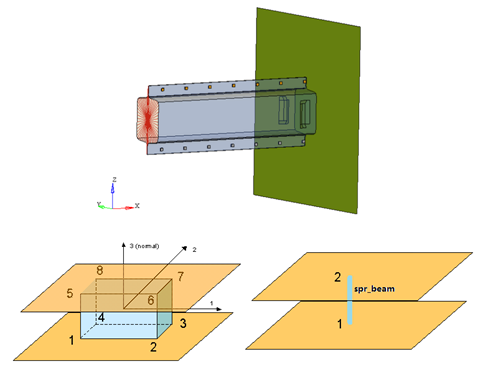
Figure 1.
Options and Keywords Used
- Rigid body and Boundary conditions
One end of the crash box is modeled using a rigid body and this rigid body is completely fixed using translations and rotations.
- Rigid wall
The impactor is modeled using a moving rigid wall having a fixed velocity (5 m/s) in a X direction and is fixed for other translations and rotations.
- Interface
The structure interaction is modeled using a TYPE7 interface on the full structure with self-impact, where the main surface is defined using the complete model and the secondary nodes group is defined using the main surface.
Input Files
- Frame Modified
- <install_directory>/hwsolvers/demos/radioss/example/48_solid_spotweld/*
Model Description
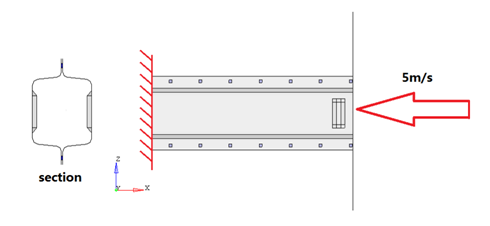
Figure 2. Problem Description and Beam Cross Section
Units: mm, s, Mg , N , MPa
- Material Properties
- Initial density
- 7.8e-9 [Mg/mm3]
- Young's modulus
- 210000
- Poisson's ratio
- 0.3
- Yield stress
- 250
- Hardening parameter
- 350
- Hardening exponent
- 0.3
In this connection material (/MAT/LAW59) use stress - plastic strain curve to describe the material characters of spot-weld. With failure model (/FAIL/CONNECT) it is possible to use two different failure criteria to describe the failure of solid spot.
- Material Properties
- Initial density
- 7.8e-9 [Mg/mm3]
- Young's modulus
- 210000
- Failure relative displacement in normal direction
- 1.0
- Failure relative displacement in tangential plane
- 1.8
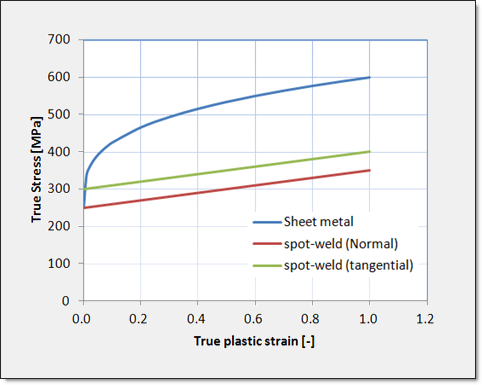
Figure 3. Material Curve of Sheet Metal and Solid Spotweld
In this example a linear behavior of spotweld has just been assumed. For more accurate results, you can also put nonlinear behavior of spotweld through real physic test and CAE validation.
Model Method
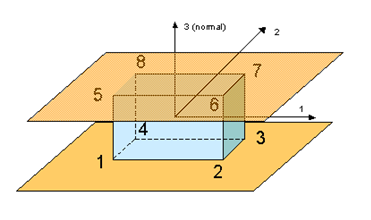
Figure 4.
- /MAT/LAW59 to define the material
- /FAIL/CONNECT to define the rupture criteria
- /PROP/TYPE43 to define the spotweld property, which should be only used with /MAT/LAW59
- /INTER/TYPE2 to define the connection between spotweld and sheet metal
- In this spotweld modeling surface 1 (Node 1, 2, 3, and 4) and surface 2 (Node 5, 6, 7, and 8) are defined. The normal direction has been defined from surface 1 to surface 2.
- Surface 1 and 2 for each solid spotweld should always connect with a shell element. If one surface of one solid spotweld is not connected with a shell element, then the stiffness will not be computed correctly and an error may occur.
Results
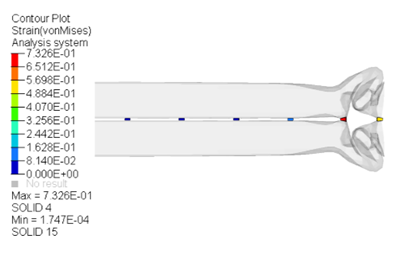
Figure 5. Strain of Solid Spotweld
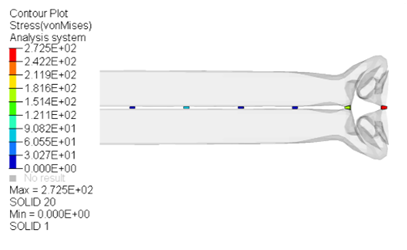
Figure 6. Stress of Solid Spotweld
Here in the model you define max. relative displacement in normal direction EPS_N_MAX=1.0 in option /FAIL/CONNECT. Therefore, two solid spotwelds (circled in red) failed after reaching this criterion.
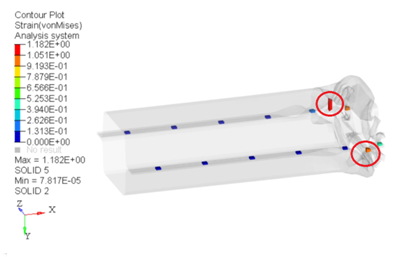
Figure 7. Strain of Solid Spotweld (display erode element in HyperView)
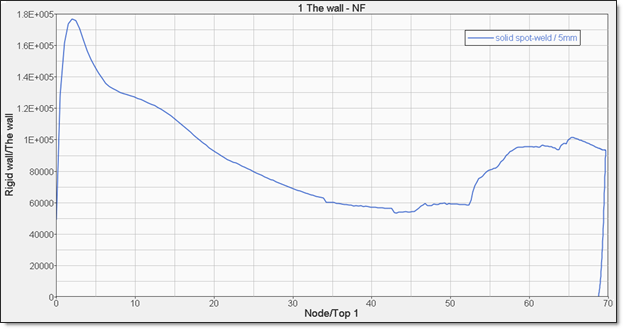
Figure 8. Force vs Displacement of Crashbox
Performance
Compared with spring beam spotweld molding, the following performance could be observed:
- With coarse sheet metal mesh size, you got
similar deformation and similar Force vs
Displacement curve for solid spotweld modeling and
spring beam spotweld modeling.
Figure 9. - Once you remesh the sheet metal shell element
with fine mesh size (for example with 2.5mm mesh
size here), then you still get similar deformation
and Force vs Displacement curve in solid spotweld
modeling but not in spring beam spotweld modeling.
This means less sheet metal mesh size dependence
for this new solid spotweld modeling.
Figure 10. - The solid spotweld element is time step is free. The element stability is assured by its nodal connection. The node of the solid element must be connected (tied interface, common nodes, and rigid connection).
- The solid spotweld element height (length in local Z direction) can be null and the spotweld results are independent from its height.
- Strain rate of solid spotweld can be taken into account.