Tied Contact (/INTER/TYPE2)
Interface TYPE2, also called tied interface is a nodal constraint to rigidly connect a set of secondary nodes to a main surface. The secondary nodes forces and moments are transferred to the main nodes, and then secondary nodes are positioned kinematically according to the motion of the main nodes.
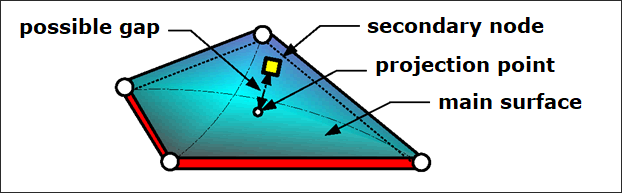
Figure 1. Interface TYPE2 - Tied
- Default spotweld formulation
- Optimized spotweld formulation
- Formulation with failure
- Penalty formulation
Default Spotweld Formulation
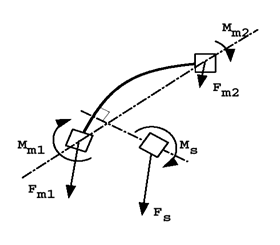
Figure 2.
- Based on element shape functions
- Generate hourglass with under-integrated elements
- Give a connection stiffness function of secondary node localization
- Recommended with fully-integrated shells (main)
- Recommended for connecting brick secondary nodes to brick main segments (mesh transition without rotational freedom)
Optimized Spotweld Formulation
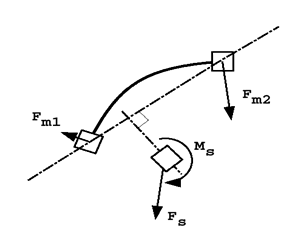
Figure 3.
- Based on element mean rigid motion
- No hourglass problem
- Constant connection stiffness
- Recommended with under-integrated shells (main)
- Recommended for connecting beam, spring, and shell secondary nodes to brick main segments
Formulation with Failure
Spotflag=20, 21 and 22
- Rupt= 0 (independent rupture parameters):
- Failure when Max_N_Dist or Max_T_Dist are reached (default)
- Rupt= 1 (coupled rupture parameters):
- Failure when
During the computation, a normal stress, shear stress, normal displacement and tangential displacement are computed and compared to the maximum values defined in the interface. As soon as the maximum criteria have been reached, the normal stress and shear stress will be set to 0.
Penalty Formulation
Spotflag=25
"INCOMPATIBLE KINEMATIC CONDITIONS".