ソリッド要素とシェル要素との接触(TYPE3)
このインターフェースは、主に当初は接触しているシェルプレートまたはソリッドプレートで使用します。
このインターフェースにはメインサーフェスとセカンダリサーフェスがありません。各サーフェスはセカンダリサーフェス相当と見なされます。
Limitations
- The two surfaces should be simply convex.
- The surface normals must face each other.
- A node may not exist on the master and slave side of an interface simultaneously.
- Surfaces must consist of either shell or brick elements.
It is recommended that the two surface meshes be regular with a good aspect ratio. The interface gap should be kept small, if not zero.
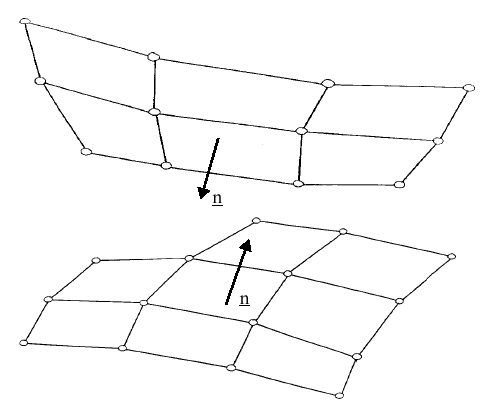
図 1. Surfaces 1 and 2 with Facing Normals
Computation Algorithm
The computation and search algorithms used for TYPE3 interface are the same as for TYPE5. However, TYPE3 interface does not have a master surface, so that the algorithms are applied twice, one for each surface.
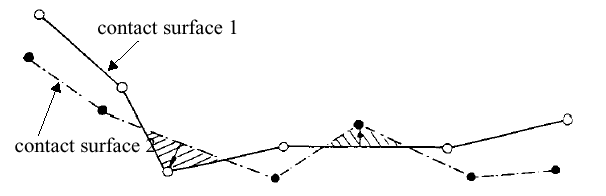
図 2. Contact Surfaces Treated Symmetrically
Because the computation algorithm is performed twice, accuracy is improved over a TYPE5 interface. However, the computational cost is increased.
The first pass solution solves the penetration of the nodes on surface 1 with respect to segments on surface 2. The second pass solves surface 2 nodes with respect to surface 1 segments.
Interface Stiffness
When two surfaces contact, a massless stiffness is introduced to reduce the penetration's nodes of the other surface into the surface.
The nature of the stiffness depends on the type of interface and the elements involved.
The introduction of this stiffness may have consequences on the time step, depending on the interface type used.
The TYPE3 interface spring stiffness K is determined by both surfaces. To retain solution stability, stiffness is limited by a scaling factor which is user defined on the input card. The default value (and recommended value) is 0.2.
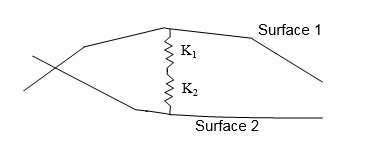
図 3. Interface Springs in Series
- Stiffness scaling factor. Default is 0.2.
- Surface 1 Stiffness
- Surface 2 Stiffness
- Overall interface spring stiffness
The scale factor, , may have to be increased if:
or
The calculation of the spring stiffness for each surface is determined by the type of elements.
For example:
implies or
Shell Element
- Modulus of Elasticity
- Shell Thickness
The stiffness does not depend on the shell size.
Brick Element
- Bulk modulus
- Segment area
- Element volume
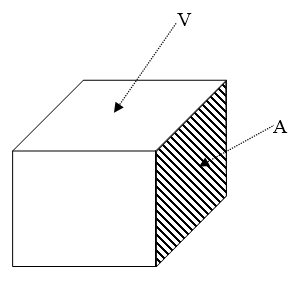
図 4. Brick Element
Combined Elements
If a segment is a shell element that is attached to the face of a brick element, the shell stiffness is used.
Interface Friction
TYPE3 interface allows sliding between contact surfaces. Coulomb friction between the surfaces is modeled. The input card requires a friction coefficient. No value (default) defines zero friction between the surfaces.
- Interface spring stiffness
- Contact node displacement vector
- Contact point at time
- Contact point at time
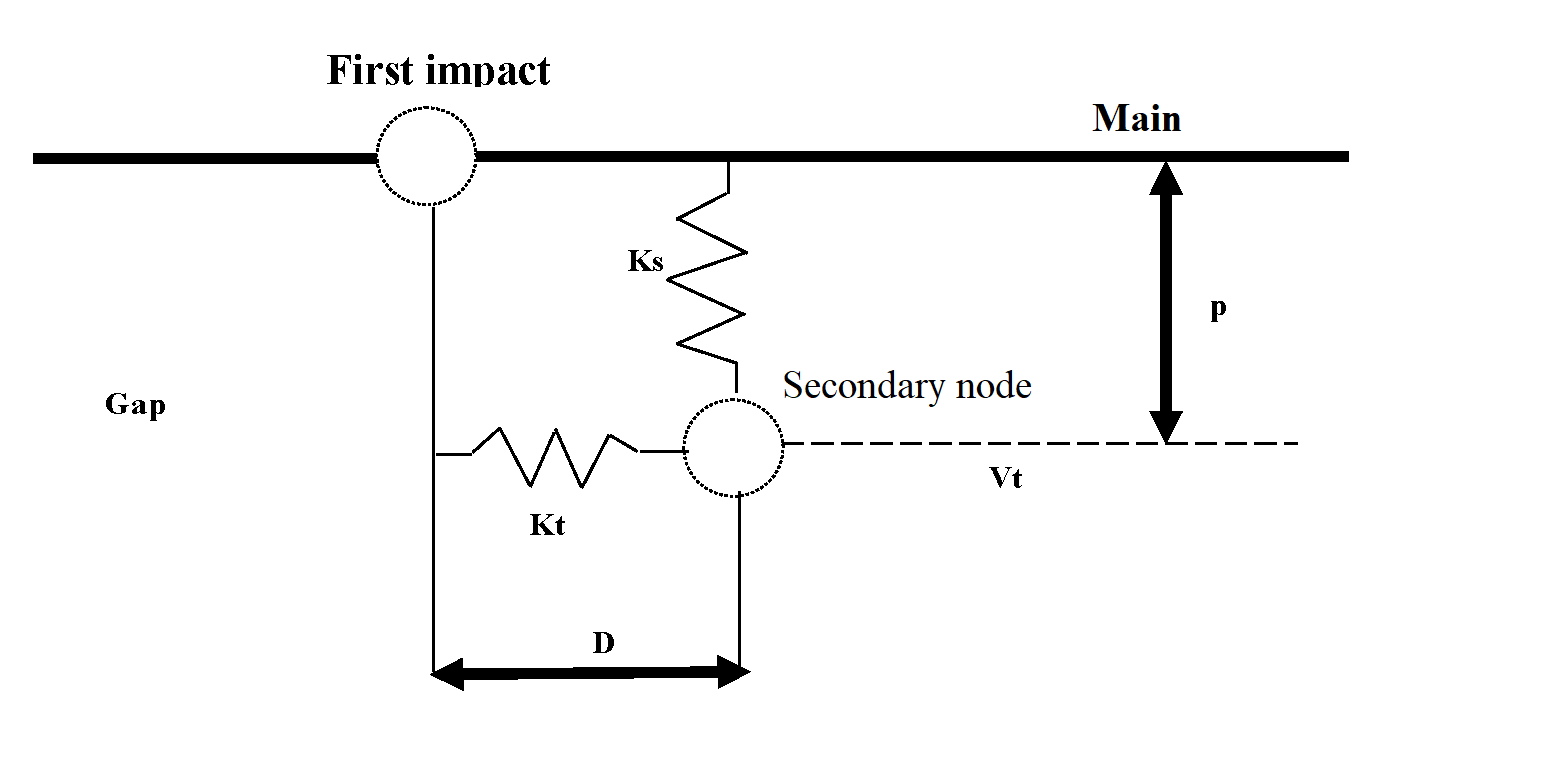
図 6. Friction on Interface TYPE3
- Initial interface spring stiffness (as in TYPE5)
Where, .
If the friction force is greater than the limiting situation, , the frictional force is reduced to equal the limit, , and sliding will occur. If the friction is less than the limiting condition, , the force is unchanged and sticking will occur.
- Result from 式 4
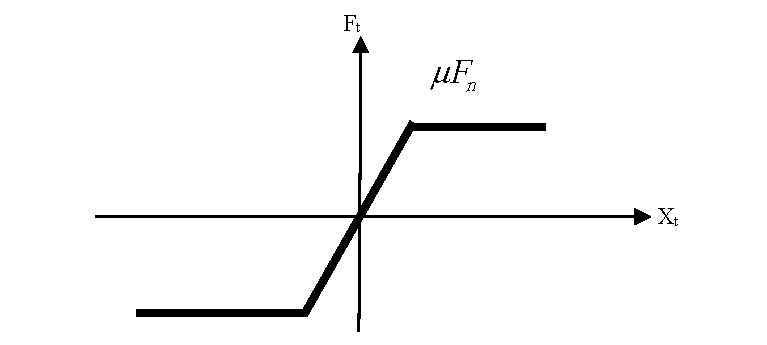
図 7. Friction on TYPE3 Interface
Interface Gap
TYPE3 interfaces have a gap that determines when contact between two segments occurs. This gap is user defined, but some interfaces will calculate an automatic default gap.
The gap determines the distance for which the segment interacts with the three nodes. If a node moves within the gap distance, such as nodes 1 and 2, reaction forces act on the nodes.
- Only normal to the segment, as shown in 図 8
- On the contact side of the segments, which is defined by the surface normal. The size of the gap defined for certain interface types is critical. If the gap is too small, the solution time step may be dramatically reduced or a node may move across the entire gap in one time step. However, if the gap is too large, nodes not associated with the direct contact may become involved.
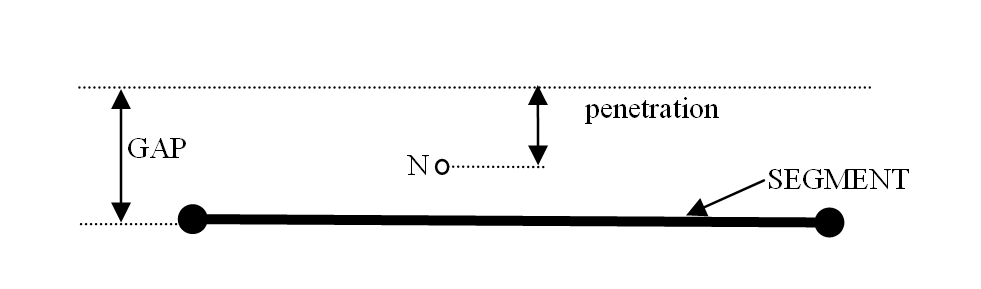
図 8. Interface Gap
Examples: Interface Failure
There are a number of situations in which TYPE3 elements may fail. A couple of these are shown below.
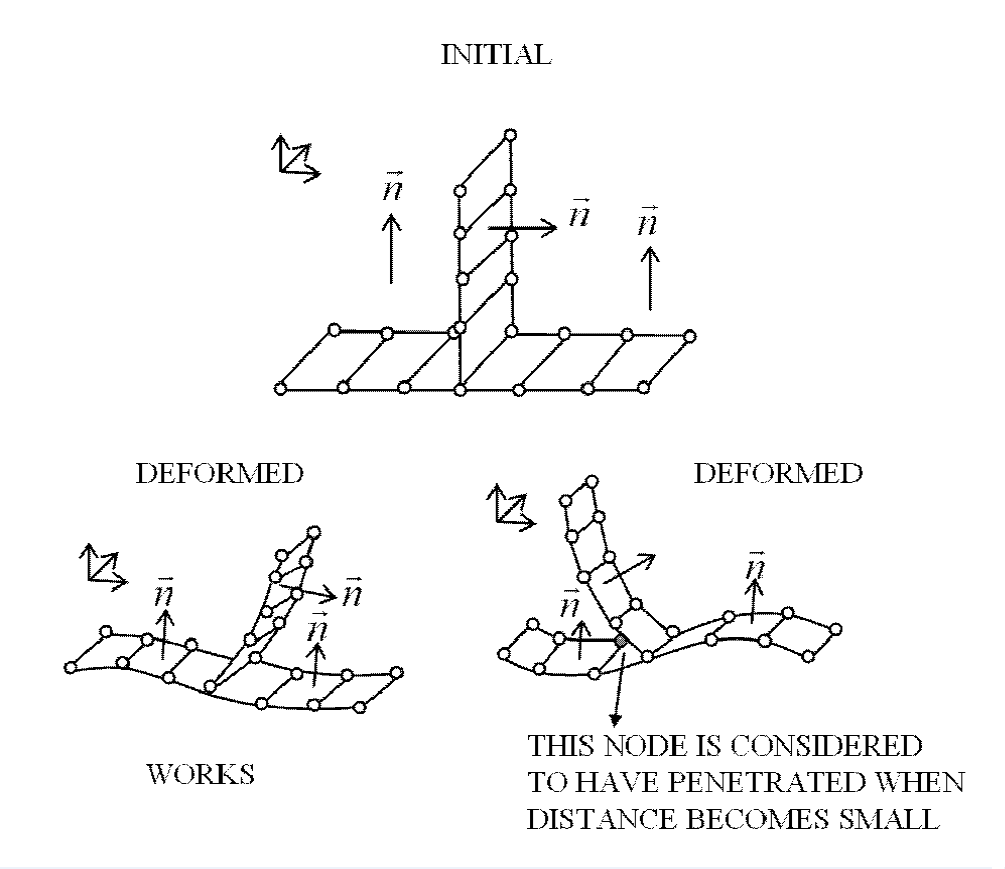
図 9. Improper Normal Direction
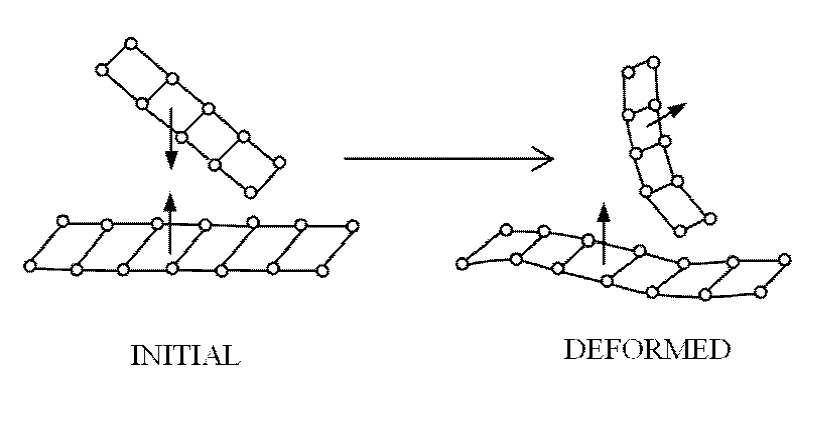
図 10. Initial and Deformed Mesh (Before Impact)
Kinematic motion may reposition the mesh so that normals do not correspond. It is recommended that possible impact situations be understood before a simulation is attempted.