Transition Flow
In the real world, laminar flow and turbulent flow coexist when obstacles are located inside of a fluid flow.
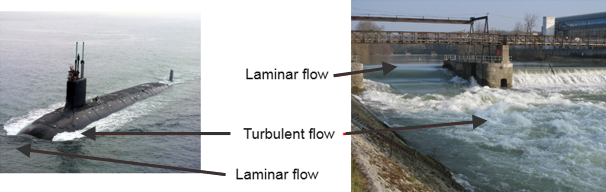
Figure 1. Submarine (left) and Dam (right)
A transition from laminar flow to turbulent flow occurs due to various external factors such as freestream turbulence level (vortical disturbances), sound waves (acoustic disturbances), temperature fluctuations (entropy disturbances), streamwise pressure gradients, surface roughness, surface curvature and vibration. Depending on the external factor or factors, the development of various transition (instability) mechanisms cause the flow to trip from laminar to turbulent. Since transition affects the flow development drag, heat transfer and many other factors it is important to understand the transition phenomena properly. The following section overviews the three main transition processes: natural transition, bypass transition and separation-induced transition.
Natural Transition
In the laminar flow regime viscous forces usually damp out the disturbances.
However, when the free stream turbulence is below one percent and the Reynolds number is higher than the critical Reynolds number, viscous forces destabilize the shear layer such that it becomes unstable two dimensional Tollmien-Schlichting (T-S) waves. These waves develop into three dimensional waves and hairpin vortices, which eventually break down, elongate, and roll up. They then develop into triangular turbulent spots past certain downstream locations. These turbulent spots grow by spreading sideways and burst into a turbulent flow.
Although T-S waves are the main instability mechanisms of the natural transition process for two dimensional boundary layers, such as flows over flat-plates, there are other kinds of instability mechanisms for natural transition. These include Görtler vortices and the crossflow instability.
Görtler vortices generate on any surfaces with concave curvatures from the effects by centrifugal forces. These are counter-rotating pairs of stationary streamwise vortices. Examples of industrial applications with concave surfaces include supercritical airfoils designed for laminar flow control, high speed wind tunnels, as well as forebody compression surfaces ahead of scramjet engine inlets. Details about these vortices are discussed in Saric (1994).
The third instability mechanism is crossflow instability. Crossflow instability develops when the pressure gradient over a swept wing combines with the cross flow from a wing root to a wing tip. It leads to the formation of three dimensional streamwise, co-rotating vortices, inducing transition.
Having an understanding of these instability mechanisms and controlling them with flow controls have received considerable attention over the past decade with the goal of delaying turbulent transition. This is beneficial in reducing the drag of slim bodies, for example wings, by keeping laminar flows as long as possible.
Bypass Transition
Another transition process is bypass transition. When the initial disturbances are high due to surface roughness or freestream turbulence levels higher than one percent, turbulent spots are generated without development of the three initial disturbances, T-S waves, spanwise vorticity and vortex breakdown, observed in the natural transition.
Although the bypass transition phenomena has been investigated in experimental and computational studies it has not been very well understood. A common industrial example of bypass transition is that of turbomachinery. The bypass transition occurs when blades in a gas turbine engine encounter wakes from upstream vanes.
Separation-Induced Transition
The third kind of transition process is separation-induced transition. When a laminar flow experiences adverse pressure gradients, such as airfoil suction surfaces and flow over a sphere, the fluid flow detaches from the wall surface.
If the disturbances are low, separation can cause the generation of structures found in natural transition. Larger disturbances generate Kelvin-Helmholtz instabilities, where vortices roll up before breaking down into turbulence. The process involved in separation-induced transition depends on the size of the adverse pressure gradient and the presence of additional disturbances, for example obstacles.
Many balls have some type of surface roughness, such as the seams on baseballs and the fuzz on tennis balls. A rough surface can assist in reducing the drag by promoting an early transition.
A number of industrial applications take advantage of this observation for practical design. These include vortex generators on various types of airfoils, such as wind turbine blades, wings and fences on aircraft and automobiles, as well as wings enhanced with surface roughness.