Refinement Zones for Commercial Heavy Trucks
This section will describe the commercial heavy truck best practice setup. Note that many of the logics and setup schemes are related to the passenger car setups. It is recommended to first read through the passenger vehicle section.
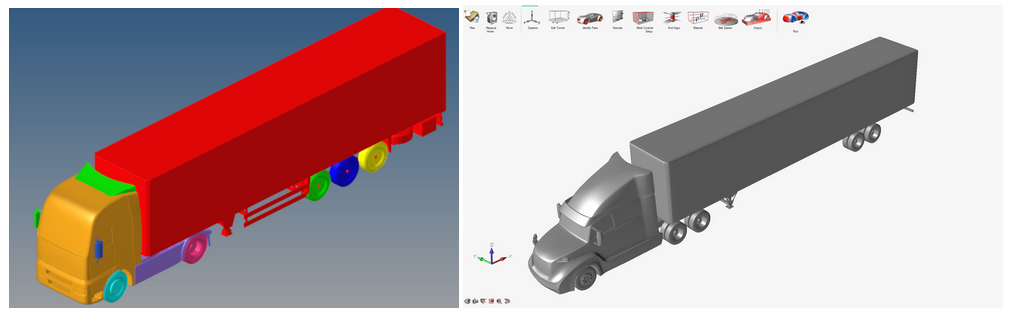
Domain and resolution levels
The Resolution Level setup is adjusted to the increased size of commercial trucks, keeping RL6 as the general offset on the whole vehicle region. Due to the larger size, an RL6 of 6mm is recommended. This would give the following resolution zones:
- RL 0: 384 mm
- RL 1: 192 mm
- RL 2: 96 mm
- RL 3: 48 mm
- RL 4: 24 mm
- RL 5: 12 mm
- RL 6: 6 mm
- RL 7: 3 mm
- RL 8: 1.5 mm
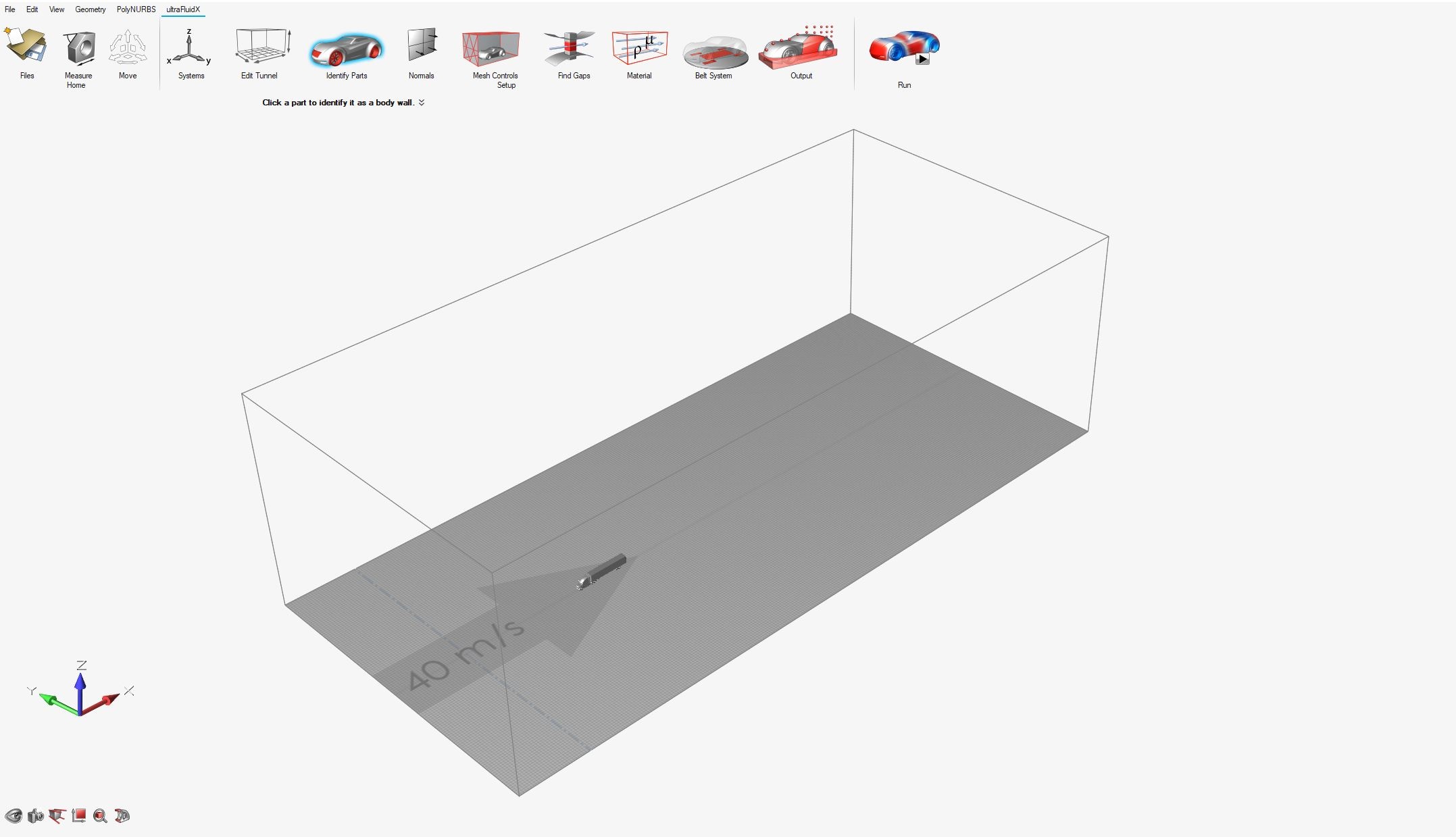
Recommended domain size tractor-trailer combination in lengths | |
---|---|
+x | 2 |
-x | 4 |
+y | 1 (or 12 widths) |
-y | 1 (or 12 widths) |
+z | 1.5 (or 20 heights) |
VWT will create a default tunnel which is sized to provide a blockage ratio of 0.5% and is adequate for standard open road simulations.
Vehicle box refinement for outer regions (RL 1 though 3)
For commercial trucks, the general resolution strategy for the outer 3 refinement regions is similar, with a shift towards the rear of the tunnel to capture the wake structures. In summary as before, it is recommended that RL1 is at least:
- X: 3 vehicle lengths downstream, 1 vehicle length upstream of the vehicle
- Y: at least one vehicle width off to the sides
- Z: at least one vehicle height above the vehicle
RL2 and RL3 are scaled down from there. It is recommended that RL3 end one length behind the vehicle.
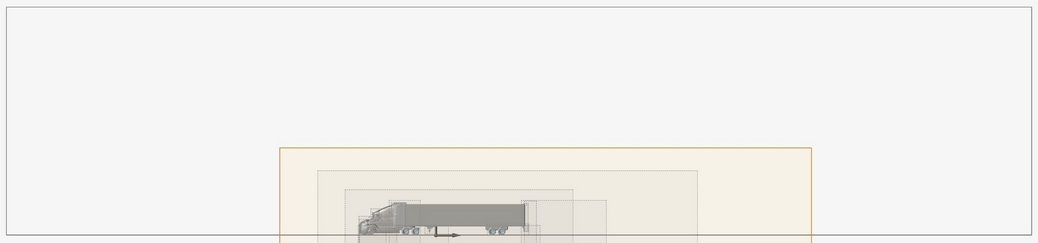
Major regions of resolution



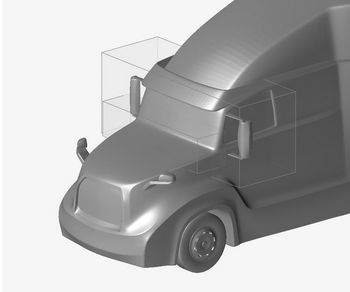
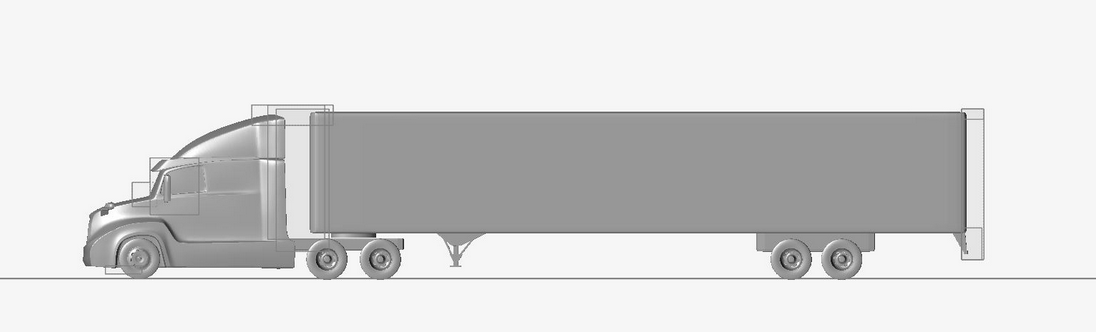
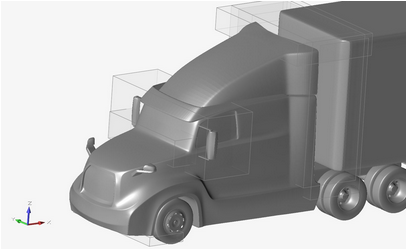
Offset refinement overall
The trailer and the aero surfaces will in general have an RL6 offset of 4 cells (4x 6mm). The engine bay and underbody in regions that do not directly touch the main underbody flow can be in RL5 if needed for voxel count reduction. Specific regions are selected for having RL7 and/or a larger number of RL6 offsets. These regions will be defined in the long-nose and cab-over sections of this chapter.
Refinement details for all trucks
The following refinement boxes or custom regions are recommended for all truck types. Please note that it is geometry dependent whether a box or a custom region is needed. Also note that some regions have already been mentioned.
- Tractor-trailer interface gaps
- The shear layer in the tractor-trailer as well as inter-trailer gaps is
important and needs to be resolved in RL6 (6mm). If the geometry is axis
aligned such that a box region suffices to capture the shear layer, this
is ok. Else a custom region can be created out of a simplified shape,
like a morphed shape.Figure 10. Regions in the interface gaps that need to be covered, in green
- Trailer base
- The base of the trailer needs to be covered all around (top, sides,
bottom including bars) using refinement boxes in RL6. This should cover
the boundary layer and the separating shear layer over the edge for the
first 0.4m.Figure 11. Resolution coverage at the base of the trailer, not the finest region around separation
- Shear layers off the front bumper
- At the bottom of the front bumper, the flow typically separates, and the
shear layer is interacting with the underbody elements of the tractor.
This shear layer should be captured in RL6 using a custom refinement
zone. Any element that is impinging the main flow should have 8 x RL6
offset voxels as well for the first 2m underneath the tractor.Figure 12. Custom zone for capturing the shear layer off the front bumper (in green), and offsets needed for impinging parts (example at green arrow)
- Cooling pack flow
- The flow through the grill elements and past the cooling pack is important. Use either a box or custom refinement region to capture this flow at least in RL5, preferably RL6.
- Treatment of the wheels
- Commercial trucks typically have more closed rims compared to passenger vehicles. For that reason, an MRF setup is not needed, and a moving wall boundary condition suffices for the rims, axles, brakes and tires.
Considerations for long-nose trucks
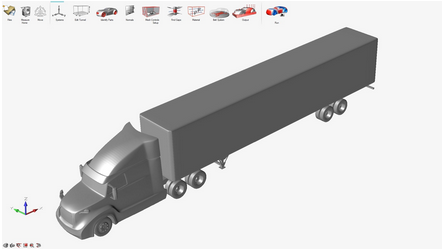
- Custom refinement regions
- It is recommended to create the following custom refinement regions:
Considerations for cab-over commercial trucks
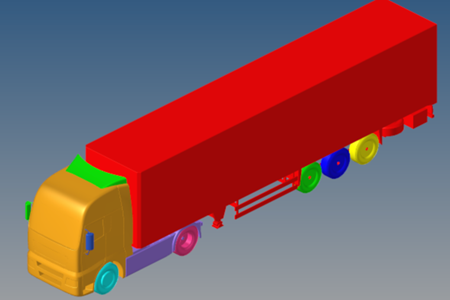
- Air curtain
- Cab-over trucks typically can have a flow deflector around the front
corners to prevent soiling onto the side-glass and door handles, called
an air curtain.Figure 18. Air curtains on cab-over trucks
- Leading edge corner flows
- For cab-over trucks, the flow around the leading-edge corners is
important. It is suggested to isolate the parts over the full height and
set a part offset of 8 layers RL7 (3mm) plus an offset of 8 layers of
RL6 (6mm) on top of that.Figure 19. Offset regions for leading edge corner flow on cab-over trucks (model source FAT)
Yaw-angle notes
The current best practices for the previous truck sections are set for 0-degree yaw angle. However, for commercial truck applications, a yaw angle (for example, 5 or 10 degrees) can be an interesting case to investigate. The leeward side of the trucks will have a large wake, which would be filled in from the top/bottom of the trailer, from leeward edges of the tractor, and from cross-flow in the tractor-trailer gap.
Considerations for yaw setups:
- The leeward edges should have a shaped refinement zone to capture the separation (RL6).
- The wake on the leeward side should be adequately captured in RL5 and RL4. This can be achieved using combined loose wraps of 0 yaw till max yaw surfaces.
- The tractor trailer gaps should have at least RL5 in the whole interface to cover cross-flow.
Run-time of the simulation
A full tractor-trailer combination is typically a lot longer than a passenger vehicle. 8 flow passes is recommended to settle the flow, and another 8 for measurement of the required variables.
For example, for a 16m long combination, inflow 25 m/s, there are 25/16=1.6 flow passes per second. The recommended setting would be:
- Total simulation time 10s
- Start of averaging time 6s (measuring between 5s and 10s)
In conclusion: mesh setup for commercial trucks
For 0 yaw, the current best practice should generate a setup of around 220-320 million voxels, which would run for 10 seconds physical time in less than 1 day on Nvidia 8 x V100 GPUs.