Altair MotionView 2021.1 Release Notes
Highlights
- Support for Pratt Miller Flexible Tire Model
- 1D Electric Powertrain with Regenerative Braking
- 1D Traction Controller for Car Library
- Other Enhancements
- Resolved Issues
Support for Pratt Miller Flexible Tire Model
MotionView v2021.1 supports a Pratt Miller flexible tire (PM-FlexTire) that can be modeled in Altair/EDEM to interact with particles representing soil, sand, gravel, and so on. The PM-FlexTire solution is available as an Altair Partner product (www.altairone.com/marketplace). MotionView allows you to set up the tire as part of vehicle modeling and transfer the tire to EDEM through the EDEM system panel.
- Tire property file (.fxt) in TeimOrbit format.
- Tire geometry file (any CAD format supported by HyperMesh).
- Handling tire property file (*.tir, *.tpf) in TeimOrbit format.
The .fxt file references the geometry and handling tire property file. The .fxt file should also contain the material properties for the tire. The handling tire is used for the initial static solution in MotionSolve and driving the vehicle over a road on a stretch that is not covered by EDEM particles.
PM_FlexTire uses a set of files (*.bdf, *.off) that provides information regarding the carcass, belt, and boundary conditions. The AutoTire panel helps in creating these files using the CAD geometry file as given in the .fxt file.
- The panel can read in a PM-FlexTire file (.fxt).
Information in the panel related to tire is automatically updated.
Figure 1. - A rim graphic with dimensions as provided in the .fxt file is available.
- Reference to a handling tire file.
- A new Flex Tire tab is available to assist you in creating the necessary
mesh files needed by PM-Flextire (Windows only).
Figure 2.
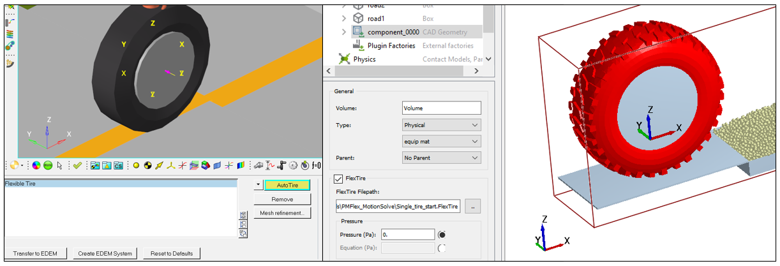
Figure 3.
- Creating of a *.FlexTire file that is used in EDEM.
- Sets the component as FlexTire and resolves the file path to the .FlexTire file.
- Includes the Rim graphic as a child of the tire component.
- Known Issues
-
- Creation of mesh files is not avaiable on Linux (PM-FlexTire software is not available on Linux).
- The AutoTire collector on the EDEM System panel does not pick the AutoTire when clicked on Tire graphics.
For additional information regarding AutoTire and the EDEM System, refer to the AutoTire - Auto Entity and Bulk Material Interaction topics in the MotionView User Guide.
1D Electric Powertrain
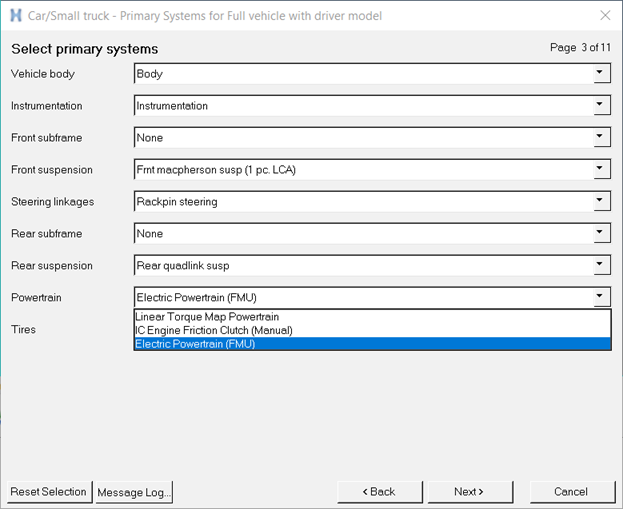
Figure 4.
The powertrain is a 1D model created in Altair Activate and exported as FMU. The Altair Activate models (.scm files) are included so you can view and edit the models to produce new FMUs as needed.
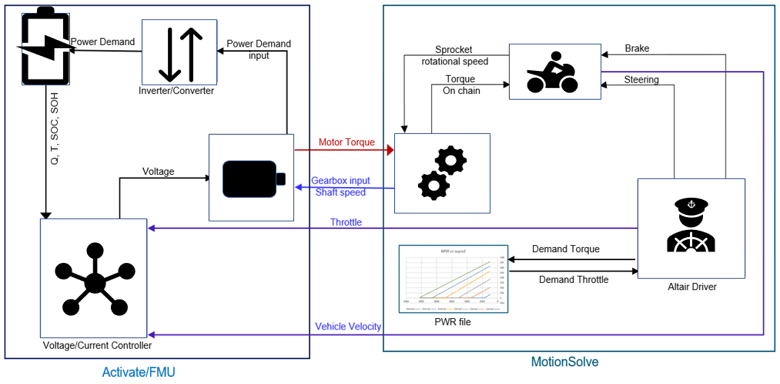
Figure 5. Interaction between Electric Powertrain (FMU) and the MotionSolve Vehicle Model
The MDL system wrapping the FMU 1D motor, inverter, and battery models includes the motor’s stationary and rotating mass and inertia, and also the battery mass and inertia which is a significant portion BEVs total mass and inertia. Finally, the electric motors’ torque-speed characteristic is read from an external file for use in Altair Driver’s feedforward speed and acceleration control.
1D Traction Controller
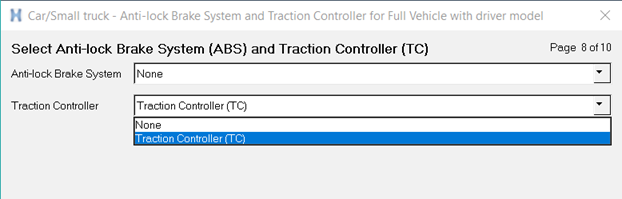
Figure 6.
The 1D TC is created in Altair Activate and exported as an FMU. The inputs to this FMU are wheel speeds, vehicle longitudinal acceleration, and Driver output throttle. The control block employs the wheel speeds and the vehicle longitudinal acceleration to estimate the tire longitudinal slips and returns (output from the FMU) the modulated throttle which is in turn used as input to the powertrain.
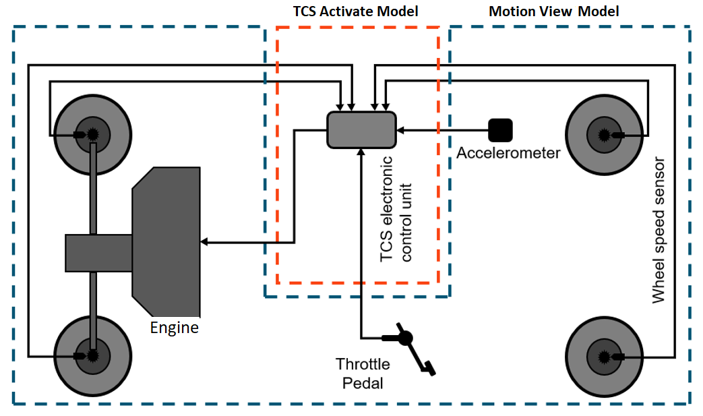
Figure 7. Interaction between Traction Controller (TC) and the MotionSolve Vehicle Model
Other Enhancements
- Data Summary
- The Data Summary tool features a new “Evaluate on Apply” option. Through this option, model evaluation can be suspended during editing data. Evaluation is done only once when either the Apply button is clicked or the entity tab is changed. This feature would be useful for editing multiple data for very large models that take significant time for model evaluation. By default, model is evaluated for every data edit.
- Spring Damper Graphic
- When a Coil Spring Damper is created, a helical shape representing the
spring and two tapered cylinders representing the damper is now displayed.
This new graphical representation replaces both the 'implicit graphic' as
well as the explicit 'SpringGraphic' options used in prior releases. The
attributes of the Spring Damper (Number of Coils, Radius) can be set in the
Spring panel. Currently the damper's inner and outer cylinders are sized as
1/3 and 2/3 of spring radius, respectively. Future releases will allow more
control over damper size with additional attributes.
- Known Issues
-
- Spring dimensions (Radius, Number of coils) of explicit SpringGraphics in legacy models are not transferred to the new Graphic tab on the Spring panel in MotionView.
- You may observe the appearance of two springs in the .h3d file (for example AutoSprings) when only one spring is expected. For instance, if your model contains an explicit SpringGraphic it will be seen along with the new Coil Spring graphic. The alternative solution for this is to either delete (or deactivate) the explicit SpringGraphic in MotionView, or you can hide it from the browser in HyperView.
- AutoSprings use the legacy explicit SpringGraphic entity
for displaying the spring in MotionView. In the current
release, this graphic is not rendered in the user
interface. Therefore, editing the graphic display
attributes "Coils" and "Coil Radius" will not show
visible changes in the user interface. However, these
change will be reflected in the simulation results
loaded in HyperView.
Figure 8. AutoSpring Panel
- Reload Curves
- A “Reload All Curves” option is available on the Curve folder, as well as System in the Model Browser, to re-read data files for all curves.
- Graphic Scaling
- The default scaling of CAD and File graphics in the Y and Z direction is now parametrized with the X direction as default. This change enhances the MotionView response while changing the scale of graphics.
- mdl_batch
- A Help option is now available on the mdl_batch command: Use
mdl_batch -help
to bring up the help content.
Resolved Issues
- Changing scale on CAD Graphics was slow in updating. The y and z scaling has been linked to x scaling as default for newly created graphics to speed up the process.
- mdl_batch on Linux failed when the path to xml contained spaces.
- mdl_batch process hangs when exporting to msolve py.
- Free point in component in contact causes failure to generate tria mesh in XML via HyperMesh.
- A Form that refers to DataSet in another System results in Errors/App Error.
- FLX referring to CMD and OBJ positioned components incorrectly when opened in HyperView.
- Update link geometry and Soil system are not displayed correctly on UHD screens.
- mview.writeFile() function does not write solver deck for ADAMS and ABAQUS solvers.
- Entities in imported system are not accessible for picking from AltairDriver attachments.
- Images related to Update Link geometry and Soil System under the Track Builder dialogs do not appear correct on an UHD screen.
- Incorrect scaling of flex bodies transferred to EDEM when using SI units.
- Negative values cannot be assigned to products of inertia through the Python API.
- DeformableCurve of the type Markers does not resolve the markers reference list in the Python API when the referenced objects are implicit markers.
- Spring damper diameter value is exported to the MotionSolve Python deck incorrectly when the spring damper radius is an expression.
- Free point in a CAD component used in contact leads to solver failure.
- Adding a report with incorrect number of arguments using View Reports results in a crash of the HyperWorks application.
- Export of FMU parameters to MotionSolve contains extra semicolon at the end.
- Application error when using a Python window with non-MotionView clients.
- Python API – writeFile() method does not write ADAMS and Abaqus solver deck.
- Python API – MotionView crash when adding a shared system.
- Python API – U array data member of FMU entity returns None.
- Python Export – Independent variable in Response variable – RMS Deviation is incorrectly written.
- Application error while editing FMU parameters.
- CSV file with headers having square braces are not read into a Curve entity.
- Connection to EDEM: Incorrect scaling of components when transferring flexible bodies from MotionView with SI units.
- CAD picking for entity creation is hard in some models.
- Curve-Surface Advanced Joints is not written to MotionSolve XML.
- Precision difference in Flexbody node and corresponding markers with MKS units causes the solver to fail.
- flexprep in batch does not work until -ospath is provided.
- NLFE preload script failed to update the NLFE body with the preload data.
- Inactive non-linear data for Force/Motion/Bushing etc. are checked that can lead to error and subsequent prevention of solver export.