Generic Heat Exchanger Component
Generic Heat Exchanger Description and Quick Guide
The Generic Heat Exchanger requires that the heat exchanger performance is known. There are several options to specify the performance such as: temperature change, thermal duty, NTU, effectiveness, and the Hs parameter.
Generic Heat Exchanger can be used in Compressible and Incompressible (hydraulic and non-hydraulic) simulations. Currently no phase change is available. The component has four fluid connections, and it models heat exchange between two streams in a network. Heat Exchangers in Flow Simulator come with 4 hidden chambers representing the 4 sides of a heat exchanger. The Generic Heat Exchanger uses Orifice or Effective Area elements (Compressible or Incompressible) in the backend to model restrictions losses (pressure loss) of both flow paths based on user defined loss parameters and characteristic flow area. The Heat addition/removal is calculated based on user inputs for Heat Exchanger Performance curves in Generic Hx module and Q (Heat Addition/Removal) is supplied to Orifice or Effective Area Elements to predict temperatures of the exiting fluids.
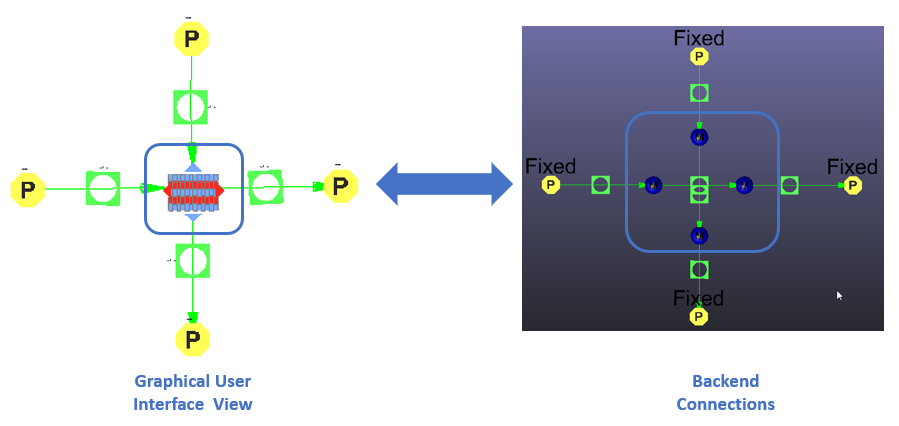
- The Hot Side circuit must get connected to Line 1 (Indicated by Red Color
part of Component Image) & Cold Side circuit get connected to Line 2
(Indicated with Blue Color part of Component Image) as shown in the image below.
- You can choose to model additional inlet and outlet losses using the separate Discrete Loss/Tube Element upstream and downstream of heat exchanger respectively.
- The Hot/Cold Side circuit line must be connected with either compressible or Incompressible set of elements. Mixing of elements sets for a Hot/Cold side circuit line is not allowed. Below Table represents some modelling/Allowable scenarios.
Modeling/Allowable Scenarios | Flow Simulator Network |
---|---|
Hot Side: Compressible Gases Cold Side: Compressible Gases Example: Air to Air Heat Exchanger |
![]() |
Hot Side : Incompressible Liquids Cold Side : Incompressible Liquids Example: Fuel Cooled Oil Cooler (FCOC) |
![]() |
Hot Side: Incompressible Liquids Cold Side: Compressible Gases Example: Air Cooled Oil Cooler (ACOC) |
![]() |
Hot Side: Compressible Gases Cold Side: Incompressible Liquids Example: Air to Liquid Heat Exchanger |
![]() |
Flow Simulator can also be used for Heat Exchanger design. For heat exchanger design a detailed representation of the heat exchanger is required. The example below shows flow elements representing the cold and hot side with thermal network resistors connecting the sides. Heat exchanger performance can be predicted from such a model.
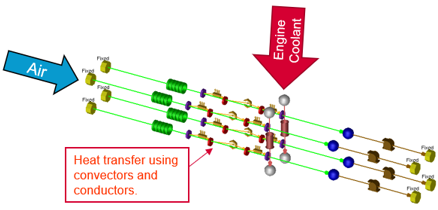
Generic Heat Exchanger Element Inputs
Table of the inputs for the Generic Heat Exchanger Component.
Element Specific Generic Heat Exchanger Component Input Variables | ||
---|---|---|
Index | UI Name (.flo label) | Description |
3,11 |
Cross Sectional Area (AREA_COLD, AREA_HOT) |
Flow area for hot & cold side fluids |
4,12 |
Hydraulic Diameter (HYD_DIA_COLD, HYD_DIA_HOT) |
Hydraulic Diameter for hot & cold side fluids |
5,13 |
Pressure Loss Options (PLOSS_COLD, PLOSS_HOT) |
Options to specify type of pressure loss modelling
|
6,14 |
Loss Coefficient (KLOSS_COLD, KLOSS_HOT) |
Incompressible Loss Coefficient |
7,15 |
Delta Total Pressure (DELTA_PT_COLD, DELTA_PT_HOT) |
Total pressure drop across a flow path |
T1, T2, T3, T4 |
Flow vs Delta P (COLD_DELTA-P, COLD_FLOW, HOT_DELTA-P, HOT_FLOW) |
|
T1, T2, T3, T4 |
Fluid Velocity vs Delta P (COLD_DELTA-P, COLD_VEL, HOT_DELTA-P, HOT_VEL) |
User Specified Curve for Fluid Velocity vs Delta.P. Delta-P table is the DIFFERENCE between the upstream driving total pressure and downstream sink static pressure |
T1, T2, T3, T4 |
Loss Coefficient vs Reynolds Number (COLD_KLOSS, COLD_REYN, HOT_ KLOSS, HOT_REYN) |
User Specified Curve for Loss Coefficient vs Reynolds Number. Reynolds Number= (4.0 * W/ (PERIM * μ)) Where:
If Hydraulic Diameter is provided, then:
If Hydraulic Diameter or Perimeter is not Provided, Reynolds
number is calculated based on Orifice Area:
|
25 | Heat Transfer Options (HOPT) |
Options for Modelling Heat Transfer between Hot & Cold side Fluids
14) Hs Constant 15) Hs vs Flow_Rate_Cold vs Flow_Rate_Hot |
26 | Heat Input (QIN) | Heat Addition |
27 | Fluid Delta.T (DELT_T) | Delta Total Temperature for Hot (or Cold) Side fluid |
28 | Effectiveness (EFFECTIVENESS) | Effectiveness of Heat Exchanger |
T4, T5, T6 |
Effectiveness vs Flow_Rate_Cold vs Flow_Rate_Hot (FLOWRATE_COLD, FLOW_HOT.., EFFECTIVENESS) |
3d Table for Effectiveness vs Flow_Rate_Cold vs Flow_Rate_Hot |
T4, T5, T6 |
Effectiveness vs NTU vs Heat Capacity Ratio (NTU, ..HEAT_RATIO, EFFECTIVENESS) |
3d Table for Effectiveness vs NTU vs Heat Capacity Ratio |
T7, T8, T9 |
Nusselt Number vs RE_Cold vs RE_Hot (NusseltNumber, ReynoldsCold, ReynoldsHot) |
3d Nusselt Number vs RE_Cold vs RE_Hot |
37 | Overall Heat Transfer Coefficient (OVERALL_HTC) | Overall Heat Transfer Coefficient Input |
29 |
Type of Configurations (CONFIG_TYPE) |
Heat Exchangers Flow Configurations
|
31 | Primary hA coefficient (PRI_HA) | Htc*Area Coefficient of Primary side fluid |
32 | Secondary hA coefficient (SEC_HA) | Htc*Area Coefficient of Secondary side fluid |
30 | Number of Shell Passes (NUM_SHELL_PASS) | No of Shell Passes for Shell & Tube Hx Configurations |
40 | Select Mixed Flow (MIXED_FLOW) |
Mixed Flow side of HX for Cross flow one side mixed option. 1=Primary, 2=Secondary |
41 | HX Area (HX_AREA) | The total heat exchanger area to be used with the Hs performance parameter |
42 |
Hs Parameter (HS_PARAMETER) |
A Heat Exchanger Performance Parameter |
Generic Heat Exchanger Theory Manual
Nomenclature: | |
---|---|
W : Mass flow rate | C: Heat Capacity |
ρ : Density | Q: Heat Addition/Rejection |
Cp : Specific Heat | Tt: Total Temperature |
NTU: Number of Transfer Units | |
Subscripts: | |
in, up, 1: Upstream station | C: Cold |
ex, dn, 2: Downstream station | H: Hot |
Pressure Loss Calculations
There are five different options through which pressure loss across hot or Cold stream can be modelled. They are:
- Fixed Loss Coefficient
- Fixed Total Pressure Drop
- Flow vs Delta.P (PTIN – PSEX)
- Velocity vs Delta.P (PTIN – PSEX)
- Loss Coefficient vs Reynolds Number
As discussed above, Generic Heat Exchanger uses Orifice or Effective Area elements (Compressible or Incompressible) in the backend to model restrictions losses (pressure loss).
To get more details on pressure drop calculation for:
- Fixed Loss Coefficient and Fixed Pressure Drop input refer to the Orifice Documentation.
- Curve based inputs (3,4,5) mentioned above refer to the Effective-Area Orifice Documentation
Heat Transfer Calculations
- Heat Input (Qin)
Tt,ex,Cold=Tt,in,Cold+QinWCold*Cpavg,Cold
Tt,ex,Hot=Tt,in,Hot−QinWHot*Cpavg,Hot
- Hot Fluid Delta.T
Q= WHot*Cpavg,Hot (Tt,in,Hot−Tt,ex,Hot)
Tt,ex,Cold=Tt,in,Cold+QWCold*Cpavg,Cold
- Cold Fluid Delta.T
Q= WCold*Cpavg,Coldt (Tt,ex,Cold−Tt,in,Cold)
Tt,ex,Hot=Tt,in,Hot−QWHot*Cpavg,Hot
- Effectiveness
CHot= ABS(WHot)*Cpavg,Hot
CCold= ABS(WCold)*Cpavg,Cold
Cmin=min(CHot, CCold)
QMax= Cmin*(Th,in−Tc,in)
Q= QMax*Effectiveness
Tt,ex,Cold=Tt,in,Cold+QWCold*Cpavg,Cold
Tt,ex,Hot=Tt,in,Hot−QWHot*Cpavg,Hot
- Effectiveness vs Flow_Rate_Cold vs
Flow_Rate_Hot
Effectiveness is obtained from User Defined Input for Effectiveness as function Flow_Rate_Cold and Flow_Rate_Hot.
CHot= ABS(WHot)*Cpavg,Hot
CCold= ABS(WCold)*Cpavg,Cold
Cmin=min(CHot, CCold)
QMax= Cmin*(Th,in−Tc,in)
Q= QMax*Effectiveness
Tt,ex,Cold=Tt,in,Cold+QWCold*Cpavg,Cold
Tt,ex,Hot=Tt,in,Hot−QWHot*Cpavg,Hot
- Effectiveness vs NTU vs Heat Capacity Ratio
Effectiveness is obtained from User Defined Input for Effectiveness as function NTU and Heat Capacity Ratio.
NTU= UACmin
CRatio= CminCmax
UA is calculated from Constant user input or from curve specified for Nusselt Number as function of Reynolds Number Cold and Reynolds Number Hot
UA= Nusselt_Number *KDh
Effectiveness=1−e((1CRatio)NTU0.22e(−CRatioNTU0.78−1))
CHot= ABS(WHot)*Cpavg,Hot
CCold= ABS(WCold)*Cpavg,Cold
Cmin=min(CHot, CCold)
QMax= Cmin*(Th,in−Tc,in)
Q= QMax*Effectiveness
Tt,ex,Cold=Tt,in,Cold+QWCold*Cpavg,Cold
Tt,ex,Hot=Tt,in,Hot−QWHot*Cpavg,Hot
- Nusselt Number vs RE_Cold vs RE_Hot
Nusselt Number is obtained from User Defined Input for Nusselt Number as function of Reynolds Number Cold and Reynolds Number Hot
UA= Nusselt_Number *KDh
NTU= UACmin
Effectiveness=1−e((1CRatio)NTU0.22e(−CRatioNTU0.78−1))
CHot= ABS(WHot)*Cpavg,Hot
CCold= ABS(WCold)*Cpavg,Cold
Cmin=min(CHot, CCold)
QMax= Cmin*(Th,in−Tc,in)
Q= QMax*Effectiveness
Tt,ex,Cold=Tt,in,Cold+QWCold*Cpavg,Cold
Tt,ex,Hot=Tt,in,Hot−QWHot*Cpavg,Hot
- Constant hA Coefficient value
CHot= ABS(WHot)*Cpavg,Hot
CCold= ABS(WCold)*Cpavg,Cold
Cmin=min(CHot, CCold)
1UA=(1h*A)Cold+(1h*A)Hot
NTU Effectiveness Methods:- Cross Flow Unmixed
Effectiveness=1−e((1CRatio)NTU0.22e(−CRatioNTU0.78−1))
- Counter Flow
Effectiveness= 1−e−NTU(1−CRatio)1−CRatioe−NTU(1−CRatio)
- Parallel Flow
Effectiveness= 1−e−NTU(1+CRatio)1+CRatio
- Cross Flow Both Side Mixed
Effectiveness= 11(1−e_NTU)+CRatio1−e−CRatioNTU−1NTU
- Cross Flow One Side Mixed
Cmin is mixed: Effectiveness=1−e−(1CRatio)(1−e−CRatioNTU)
Cmax is mixed: Effectiveness= (1CRatio)(1−e−(CRatio(1−e_NTU)))
QMax= Cmin*(Th,in−Tc,in)
Q= QMax*Effectiveness
Tt,ex,Cold=Tt,in,Cold+QWCold*Cpavg,Cold
Tt,ex,Hot=Tt,in,Hot−QWHot*Cpavg,Hot
- Cross Flow Unmixed
- Hs Parameter Methods (Constant and vs Hot and Cold
Flowrates)
The Hs parameter is typically used to describe radiators where the hot side is a liquid coolant, and the cold side is air.
Hs=ABS(WHot)*Cpavg,Hot*(Th,in−Th,ex)HXArea*(Th,in−Tc,in)
Hs*HXArea*(Th,in−Tc,in)=ABS(WHot)*Cpavg,Hot*(Th,in−Th,ex)=Q
A heat exchanger effectiveness can be calculated using the Hs parameter.
Effectiveness=Q / QMax
QMax= Cmin*(Th,in−Tc,in)
Effectiveness=Hs*HXArea*(Th,in−Tc,in)Cmin*(Th,in−Tc,in)=Hs*HXAreaCmin
Q is found using the effectiveness Qmax. The Q is applied to the fluid streams to get the exit temperatures.
Tt,ex,Cold=Tt,in,Cold+QWCold*Cpavg,Cold
Tt,ex,Hot=Tt,in,Hot−QWHot*Cpavg,Hot
Generic Heat Exchanger Outputs
The following listing provides details about Generic Heat Exchanger Component output variables.
Name | Description | Units |
---|---|---|
PS | Static pressure | psia, MPa |
PT | Total pressure | psia, MPa |
TT | Total temperature of fluid | deg F, deg K |
RE | Reynold Number | (None) |
Rho | Density | lbm/ft^3, Kg/m^3 |
CP | Specific Heat | Btu/(Lbm R), kJ/Kg.K |
K | Thermal Conductivity | Btu/(hr ft R), W/m.K |
DVISC | Dynamic Viscosity | Lbm/(hr ft), N s/m^2 |
Area | Flow Area | In2, m2 |
Heat Mode |
Heat Mode Options (An echo of the user input)
|
(None) |
Pri/cold_side_ploss_opt |
Options specified for Pressure Loss Modelling for Pri/Cold side
(An echo of the user input) |
(None) |
Sec/hot_side_ploss_opt |
Options specified for Pressure Loss Modelling for Sec/Hot side
(An echo of the user input) |
(None) |
Q | Heat Transferred between Heat Exchanger fluids. | BTU/sec, W |
Effectiveness | Effectiveness of Heat Exchanger | (None) |
Pri/cold_side_delta.p | Delta.PT on Pri/Cold side flow | psia, MPa |
Sec/hot_side_delta.p | Delta.PT on Sec/Hot side flow | psia, MPa |
Mdot | Mass Flow Rate | Lbm/s, kg/s |
Flow configuration |
Heat Exchangers Flow Configurations
(An echo of the user input) |
(None) |
Overall conductance(UA) | Overall Thermal Resistance | BTU/hr.F, W/K |
NTU | No of Transfer Units | (None) |
Pri_hA_out | Pri/Cold side flow hA Coefficient value | BTU/hr.F, W/K |
Sec_hA_out | Sec/Hot side flow hA Coefficient value | BTU/hr.F, W/K |