Stamping
A stamping constraint should be used when the manufacturing process calls for stamping rather than casting.
A stamping constraint can be applied from the part context menu.
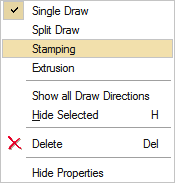
This type of constraint should be used when the manufacturing process calls for stamping rather than casting. When you run an optimization on a design space with a stamping constraint applied, the solver returns a result with uniform thickness while avoiding negative draft angles and internal voids.
When applying a stamping constraint, you may also specify the No Hole option in the microdialog to eliminate internal voids. Stamping constraints are valid for optimization but not analysis.
Apply a Stamping Constraint
Click on a design space and use the context menu to apply a stamping constraint.
Microdialog Options
Double-click a shape control to edit it and access the microdialog options.
Icon | Description |
---|---|
Apply Draw Direction | Click to convert the stamping constraint to a different type of draw direction. |
![]() |
Eliminate internal voids in the optimized part. |
![]() |
Flip the draw direction. |
![]() |
Rotate the shape control. |
![]() |
Align a shape control to a design space after moving it. By default, shape controls are aligned to capture the most likely orientation for that particular design space as it is oriented in space. |
![]() |
Align a shape control to the global axes. |
Stamping Examples
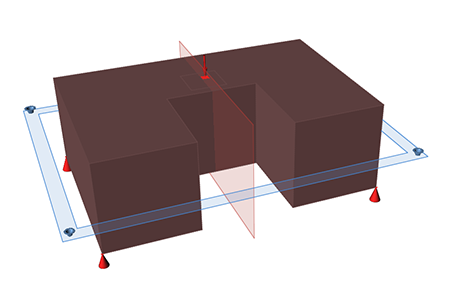
Figure 1. Design Space
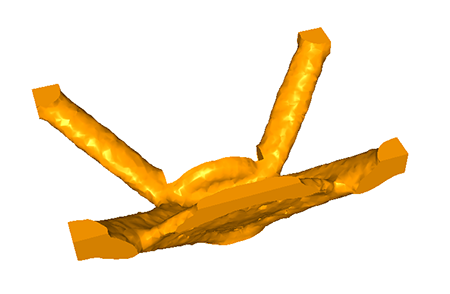
Figure 2. Optimized Shape with Stamping Applied
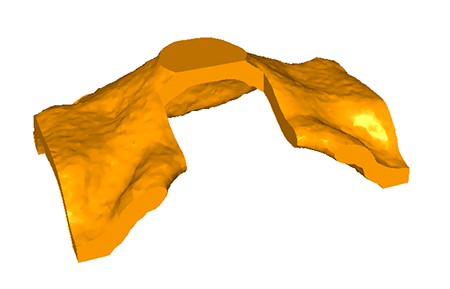
Figure 3. Optimized Shape with Stamping Applied and No Holes