Strain-Life (E-N) Approach
The E-N Approach uses plastic-elastic strain results to perform strain-life analysis.
Strain-life analysis is based on the fact that many critical locations such as notch roots have stress concentration, which will have obvious plastic deformation during the cyclic loading before fatigue failure. The elastic-plastic strain results are essential for performing strain-life analysis.
Neuber Correction
Neuber correction is the most popular practice to correct elastic analysis results into elastic-plastic results.
In order to derive the local stress from the nominal stress that is easier to obtain, the concentration factors are introduced such as the local stress concentration factor KσKσ , and the local strain concentration factor KεKε .
Where, σσ is the local stress, εε is the local strain, S is the nominal stress, and e is the nominal strain. If nominal stress and local stress are both elastic, the local stress concentration factor is equal to the local strain concentration factor. However, if the plastic strain is present, the relationship between KσKσ and KεKε no long holds. Thereafter, focusing on this situation, Neuber introduced a theoretically elastic stress concentration factor KtKt defined as:
Substitute Equation 1 and Equation 2 into Equation 3 the theoretical stress concentration factor KtKt can be rewritten as:
Through linear static analysis, the local stress instead of nominal stress is provided, which implies the effect of the geometry in Equation 4 is removed, thus you can set KtKt as 1 and rewrite Equation 4 as:
Where, σeσe , εeεe is locally elastic stress and locally elastic strain obtained from elastic analysis, σσ , εε the stress and strain at the presence of plastic strain. Both σσ and εε can be calculated from Eq.9 together with the equations for the cyclic stress-strain curve and hysteresis loop.
Cyclic Stress-Strain Curve
- Stable state
- Cyclic hardening
- Cyclic softening
- Softening or hardening depending on strain range
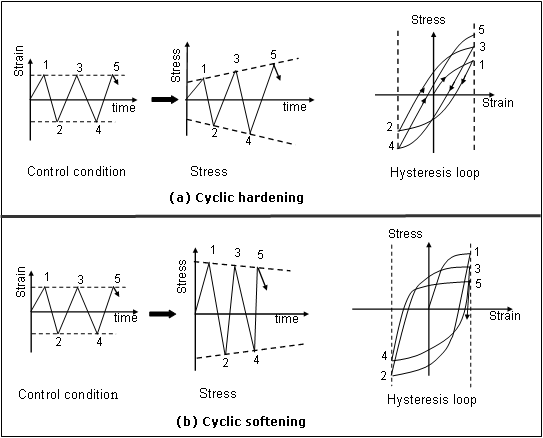
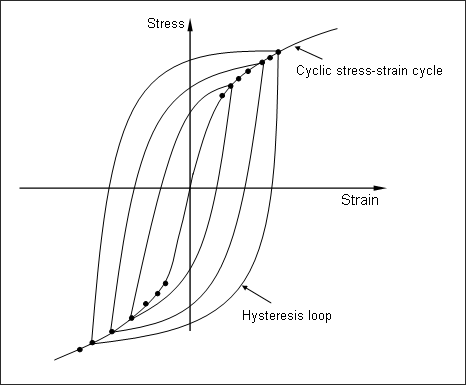
This can be expressed in the similar form with monotonic stress-strain curve as:
Hysteresis Loop Shape
Bauschinger observed that after the initial load had caused plastic strain, load reversal caused materials to exhibit anisotropic behavior. Based on experiment evidence, Massing put forward the hypothesis that a stress-strain hysteresis loop is geometrically similar to the cyclic stress strain curve, but with twice the magnitude. This implies that when the quantity (Δε, Δσ) is two times of (ε, σ) , the stress-strain cycle will lie on the hysteresis loop. This can be expressed with formulas:
Expressing σ in terms of Δσ , ε in terms of Δε , and substituting it into Equation 6, the hysteresis loop formula can be calculated as:
Almost a century ago, Basquin observed the linear relationship between stress and fatigue life in log scale when the stress is limited. He put forward the following fatigue formula controlled by stress:
Where, σa is stress amplitude, σ'f fatigue strength coefficient, b fatigue strength exponent. Later in the 1950s, Coffin and Manson independently proposed that plastic strain may also be related with fatigue life by a simple power law:
Where, εpa is plastic strain amplitude, ε'f fatigue ductility coefficient, fatigue ductility exponent. Morrow combined the work of Basquin, Coffin and Manson to consider both elastic strain and plastic strain contribution to the fatigue life. He found out that the total strain has more direct correlation with fatigue life. By applying Hooke Law, Basquin rule can be rewritten as:
Where, εea is elastic strain amplitude. Total strain amplitude, which is the sum of the elastic strain and plastic stain, therefore, can be described by applying Basquin formula and Coffin-Manson formula:
Where, εa is the total strain amplitude, the other variable is the same with above.
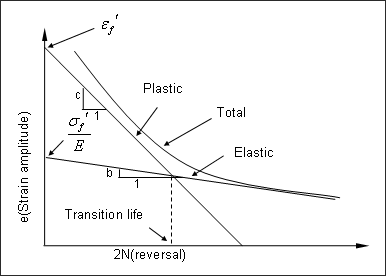