Tutorial: Hollow Profile Extrusion
Set up and complete a hollow profile extrusion analysis and post-process the data.
Model contains madrel and die cap. Two hollow profiles are being extruded through this die assembly. Data files are available in the tutorial_models folder in the installation directory in Program Files\Altair\2021\InspireExtrudeMetal2021\tutorial_models\extrudemetal\tutorial-2\.
Import and Orient Die Solids
Extract Flow Volume
-
Click the Flow Volume icon to extract flow volume inside
of the die cavity.
-
Click and hold left mouse button while you drag a box around all the die solids
as shown.
-
Release left mouse button to extract flow volume automatically.
Combine Flow Volume
-
Hold CTRL and click on each flow solid as shown.
-
Right-click on either selected solid and click
.
Extract Bearing Region
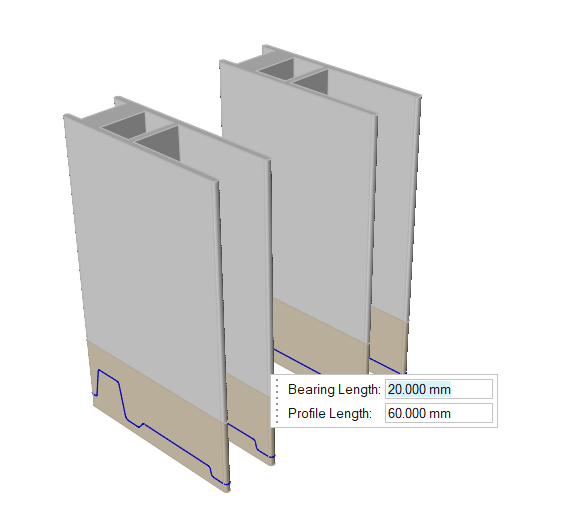
Organize Flow Volume
-
Click the Organize Volumes based on Length Icon.
-
A micro dialogue will pop up, where you must enter the following
measurements:
- Press OK to close the window.
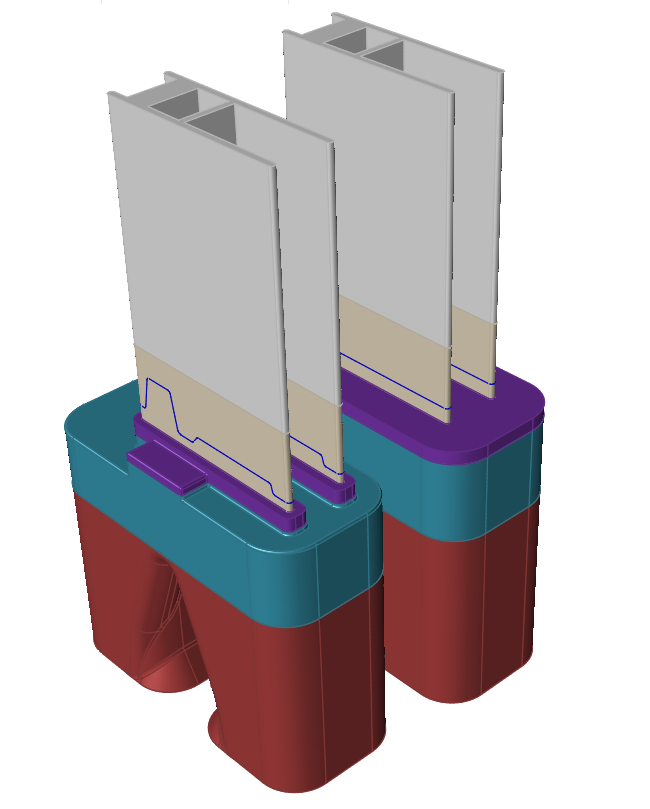
Create the Billet
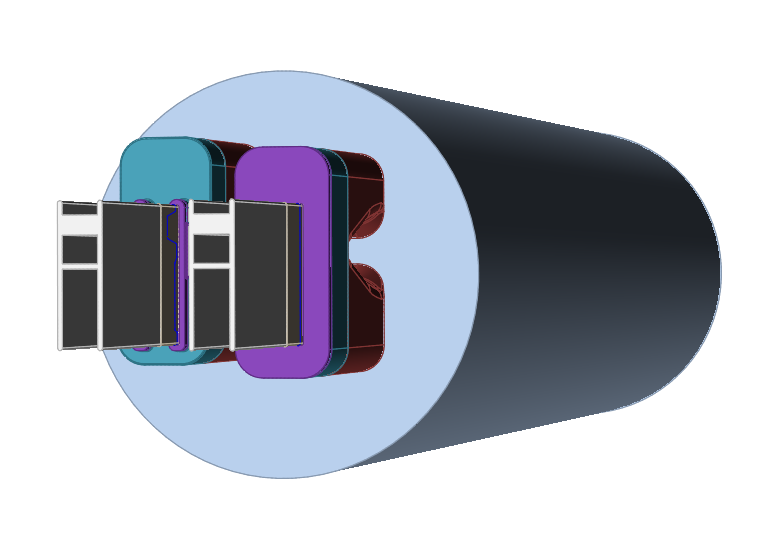
Select the Material
Specify Process Parameters and Simulate
-
Click theSubmit job for analysis icon to run the
simulation.
-
In the Analysis Parameters window that pops up, enter
values as shown.
- Click the Run button.
Status after submitting the job |
![]() |
Status after meshing is completed |
![]() |
Status when job is running in the solver |
![]() |