In this tutorial, you will:
• | Understand the data in the .out file through analysis |
• | Load the h3d file from the analysis in HyperView |
• | Plot a displacement contour |
• | Plot a velocity contour with section cuts to observe the flow pattern in the die |
• | Plot a vector plot of the results |
• | Plot a temperature contour |
The model files for this tutorial are located in the file mfs-1.zip in the subdirectory \hx\MetalExtrusion\. See Accessing Model Files.
To work on this tutorial, it is recommended that you copy this folder to your local hard drive where you store your HyperXtrude data, for example, “C:\Users\HyperXtrude\” on a Windows machine. This will enable you to edit and modify these files without affecting the original data. In addition, it is best to keep the data on a local disk attached to the machine to improve the I/O performance of the software.
|
1. | Run the solver. The solution convergence history is saved in the file jobname_000.out. |
2. | Open the file HX_0501_000.out in a text editor. |
3. | Check if the Extrusion Ratio is correct. If not, check the BCs. |
4. | Check the Norm on Change in Solution to see whether Velocity, Temperature, and Pressure are decreasing from one iteration to the next. |
This may oscillate initially, but it will decrease steadily after the initial iterations. The solution is converged if the value of Norm of Change in Solution is less than 0.001.
A slow convergence rate or oscillatory behavior indicates the mesh is too coarse. Fix the problem before proceeding to the next step.
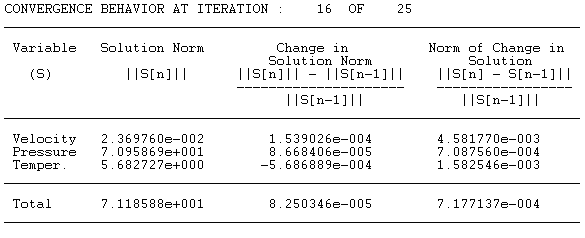
|
1. | Check if the Mass Balance is less than 1%. |
• | Extrusion speed at Outflow boundary (Uexit) must be equal to Extrusion _Ration*Uram |
• | Velocity on solid walls must be close to zero. |
• | Velocity on symmetry planes must be equal to zero. |
• | Velocity on free surface and bearing walls must be small (at least less than four orders of magnitude less than the extrusion speed). |
• | The Mass Flux table shows mass flow rate across each boundary. A positive sign indicates material entering through the boundary, and a negative sign indicates material leaving the boundary. The table also contains average velocity of the material entering/leaving through each boundary surface. |
2. | If any of these checks fail, verify the boundary conditions. |
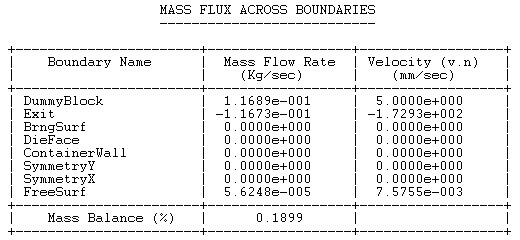
|
The Heat Flux table shows heat transfer rate across each boundary. A positive sign indicates energy input to the system, and a negative sign indicates energy leaving through the boundary. The table also contains average temperature at each boundary surface.
1. | Check if energy balance is < 5%. |
2. | Check if average temperatures are within an acceptable range. |
3. | Verify the boundary conditions and material properties, if either one of these checks fail. |
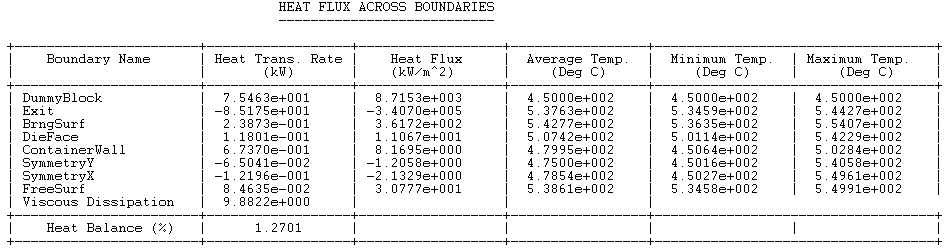
|
A positive sign indicates force applied on a surface, and a negative sign indicates response. The table also contains average pressure at each boundary surface.
1. | Check if each component of total force vector is in equilibrium (< 5%). |
2. | Check if average pressure at Ram (inlet) is within an acceptable range. |
3. | Verify the boundary conditions and material properties if either one of these checks fail. |
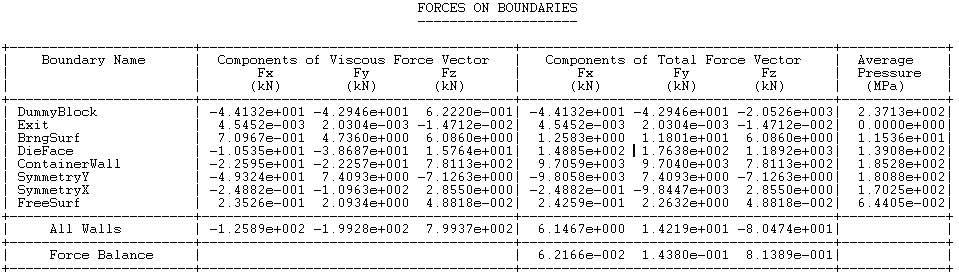
|
The amount of heat generated during deformation must be equal to the mechanical work.
1. | Check if Viscous Dissipation - Ram Force * Ram Speed * % of mechanical energy converted to heat < 5%. |
|
The Norm of Mesh Displacement quantifies the amount of profile deflections. Large values indicate that the velocities at die exit are not uniform and this produces large profile deflections.
• | If Norm of Mesh Displacement < 0.1, then the flow is balanced and die design is acceptable. |
• | If 0.01 < Norm of Displacement < 0.1 continue additional solution steps to see if the profile deflection calculations converge. Use the profile deflections to correct the die. |
• | If Norm of Mesh Displacement > 0.1, stop the analysis and correct the die. |
|
1. | Copy the H3D file HX_0501_000.h3d to your working directory. This file contains the finite element mesh for workpiece, material properties, and boundary conditions. |
2. | Load the H3D file into HyperView. |
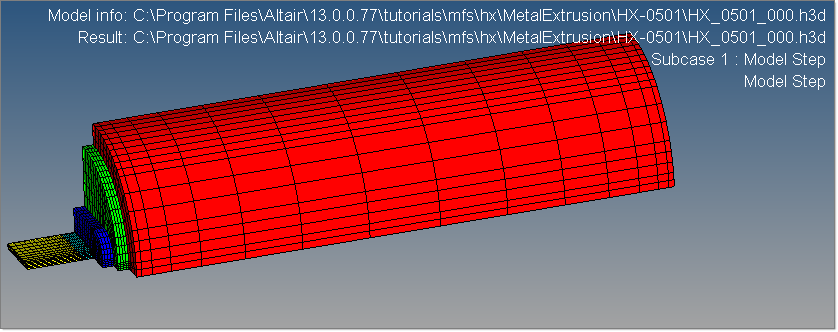
|
1. | Go to the Contour panel in HyperView. |
2. | For Result type, select Displacement. |
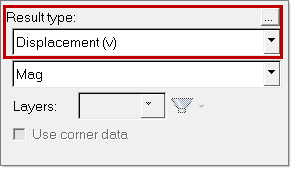
3. | Click on the load case and simulation sequence at the bottom and select Mesh Update Step = 1. |
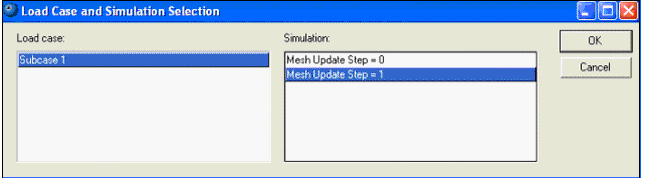
4. | Click Apply. The contour shows the displacement of the profile. |
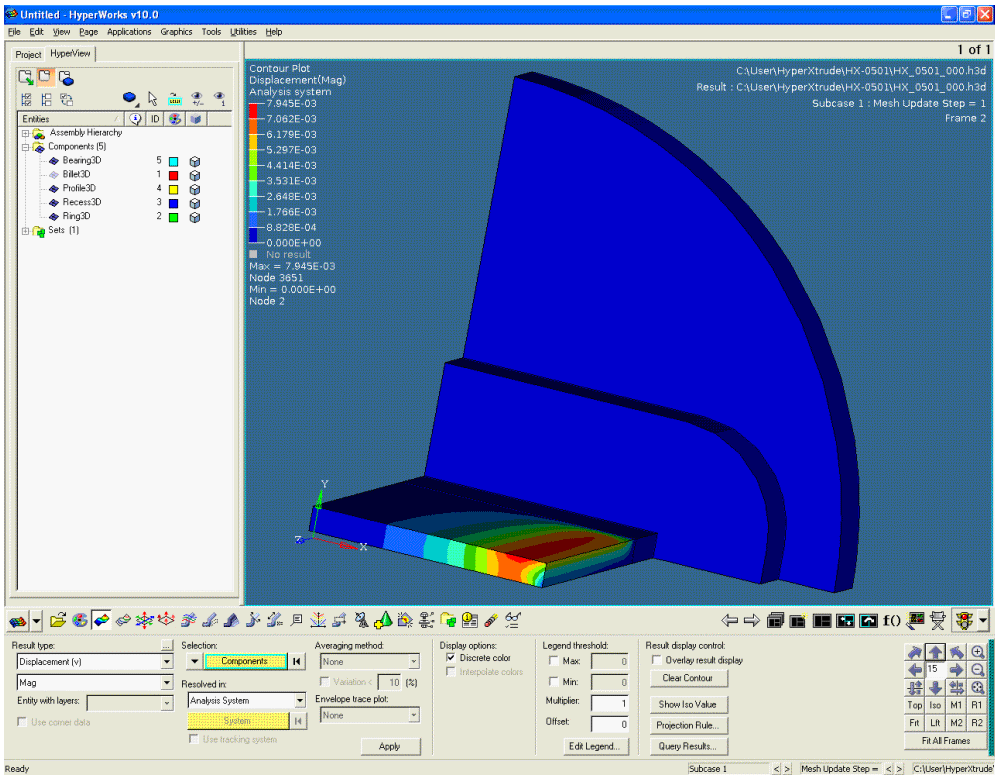
|
1. | On the Graphics menu, click Entity Attributes. |
2. | Turn off the components Billet3D and Profile3D. |
3. | Go to the Contour panel in HypeView. |
4. | For Result type, select Velocity. |
6. | On the Graphics menu, click Section Cut. |
7. | Create sections at different locations in the pockets in the Z axis. Notice the flow pattern in the pockets. |
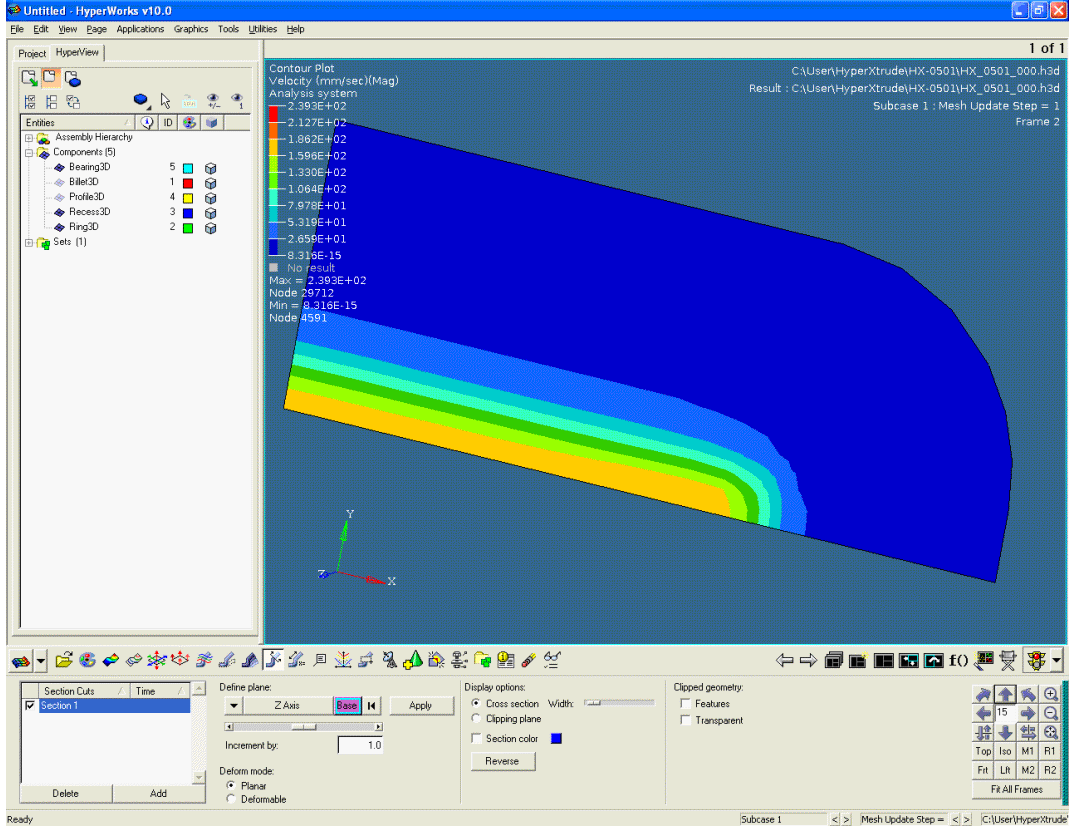
|
1. | On the Graphics menu, click Vector. |
2. | Under Selection: click Components and select All. |
3. | For Size scaling, select Uniform. |
4. | For Show, select Resultant. |
5. | Click Apply to display vectors that show the flow. |
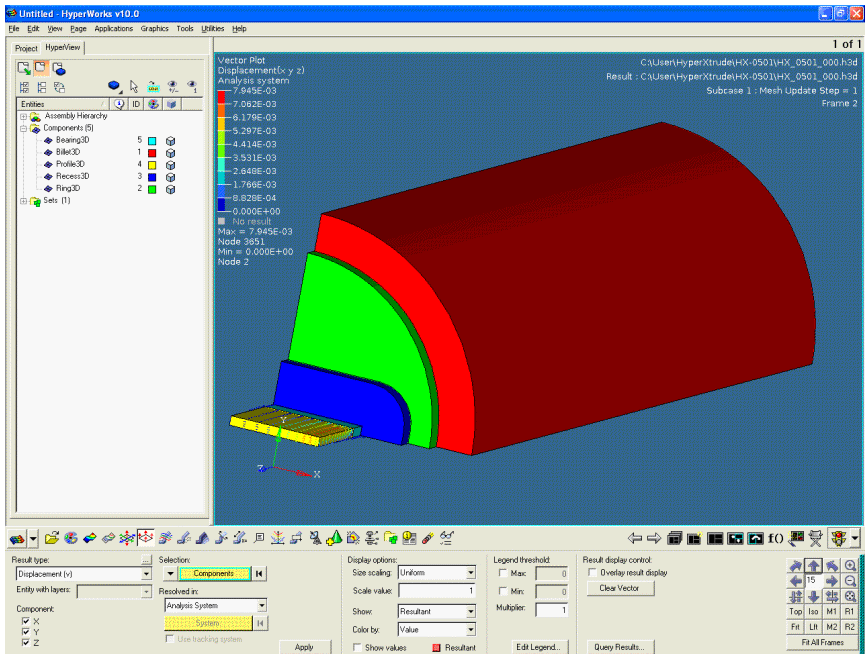
|
1. | Turn on all components in the Entity Attributes panel . |
2. | Go to the Contour panel . |
3. | For Result type:, select Temperature. |
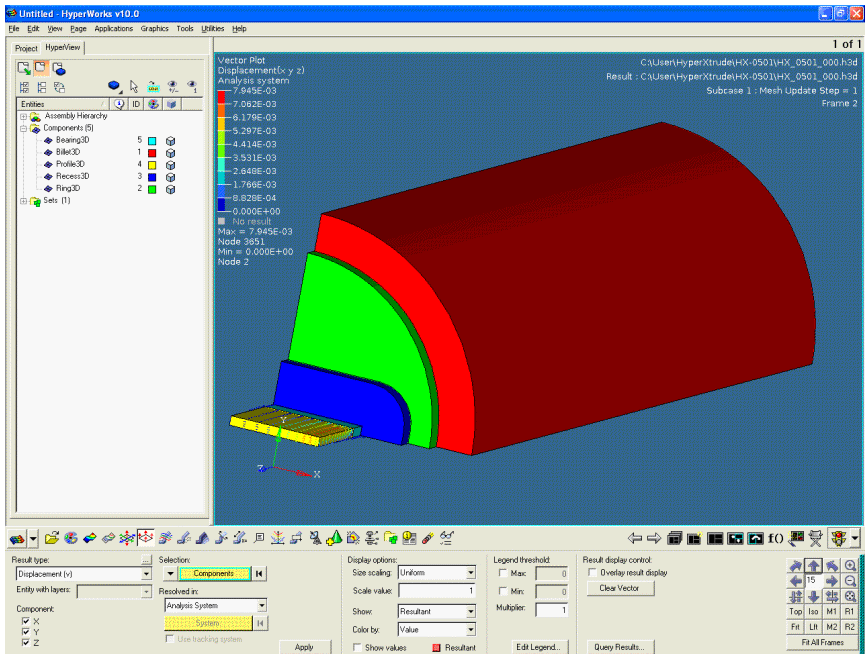
|
Return to Metal Extrusion Tutorials