In this tutorial, you will learn how to create a finite element mesh for a hollow profile extrusion analysis from the 3D CAD file. Profiles are often classified as solid, semi-hollow, and hollow. Die assembly used for both hollow and semi-hollow profile extrusion includes die cap and die mandrel. The die cap is often simply referred to as die and the die mandrel as mandrel. Die cap defines the outer perimeter of the profile shape and the die mandrel defines the inner perimeter of the hollow regions. The cavity (the flow region in the die through which material flows and deforms) formed by the mandrel is called port holes and by the die cap is called weld chamber. This is because the material divides and flows into multiple ports in the port hole region and comes back to weld together in the weld chamber. Often, due to the complexity of the geometry in the weld chamber region, automatic meshing may require finer mesh size to create a good quality mesh.
Outline of the tutorial
1. | Load the HyperMesh file and inspect the model |
Note: The model files for this tutorial are located in the file mfs-1.zip in the subdirectory \hx\MetalExtrusion\HX_0023. See Accessing Model Files.
To work on this tutorial, it is recommended that you copy this folder to your local hard drive where you store your HyperXtrude data, for example, “C:\Users\HyperXtrude\" on a Windows machine. This will enable you to edit and modify these files without affecting the original data. In addition, it is best to keep the data on a local disk attached to the machine to improve the I/O performance of the software.
1. | Select Start Menu > All Programs > Altair HyperWorks > Manufacturing Solutions > HyperXtrude to launch the HyperXtrude user interface. The User Profiles dialog appears with Manufacturing Solutions as the default application. |
2. | Select HyperXtrude and Metal Extrusion. |
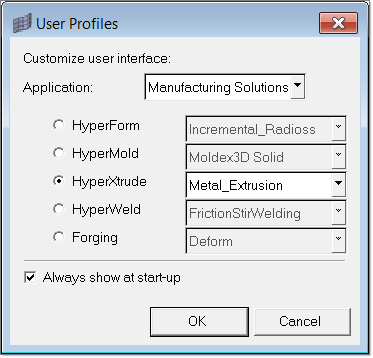
|
1. | From the File menu, click Open. |
2. | Use the file browser to select the file HX_0023.hm |
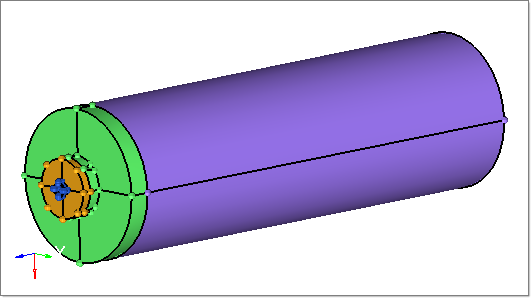
This model contains four components: Billet, Porthole, WeldingChamber, and Bearing. The Porthole component also contains the feeder region in this mesh.
|
In this step you will create components to save the Billet, Bearing and Profile elements.
1. | In the Model browser, right-click on Component and select Create. |
2. | In the Create Component dialog, enter the component name as Billet3D, select a color for the component, and click Create. |
3. | Repeat steps 1 and 2 to create the components Portholes3D, WeldChamber3D, Bearing3D and Profile3D. The Model browser shows the list of all the components in the model. |
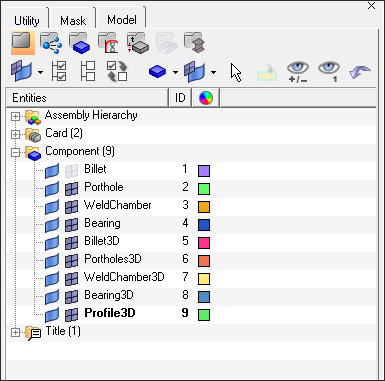
|
1. | In the Model browser, right-click on the Bearing component and select Isolate. This hides the display of the other components in the model. |
2. | Click on the graphics area and click f to fit the model into the graphics area. |
3. | Click the Shaded Geometry and Surface Edges icon to change the display of the component. |
4. | From the main menu, select the automesh button. |
5. | Click the surfs button and select the surface shared by the Bearing and WeldChamber. |
6. | Set the mesh type field to trias, and enter 0.35 in the element size field. |
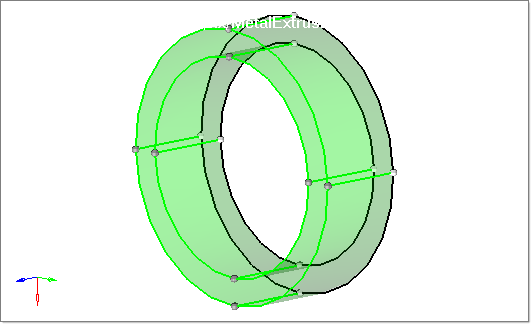
7. | Click mesh to create the surface mesh. This creates mesh with at least 5 elements through the thickness of the profile. |
8. | Click return twice to close the panel. |
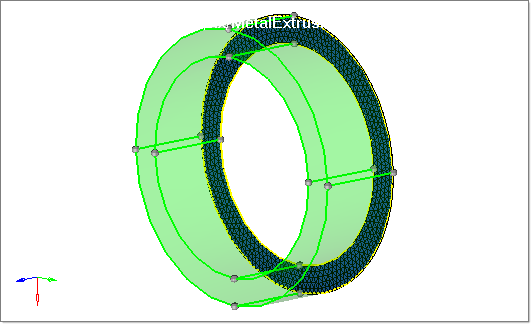
9. | In the Model browser, right-click on Bearing3D and select Make Current. Right-click again and select Show. |
10. | From the main menu, select drag. |
11. | Select the drag elems subpanel and select Z-axis for the drag direction. |
12. | Click elems >> displayed. |
13. | Set the distance = field to 5, enter 10 in the on drag = field, and click drag+ to create 3D elements in bearing region. |
14. | Click return to close the panel. |
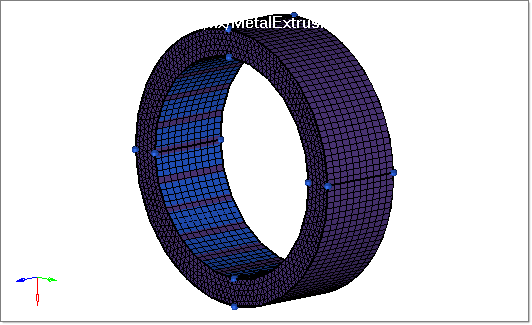
|
1. | In the Model browser, right-click on the Porthole component and select Isolate. |
2. | Right-click on the Portholes3D component and select Make Current. Right-click again and select Show. |
3. | From the main menu, select tetramesh. |
4. | Select the volume tetra subpanel for meshing. |
5. | Click solids and select the Porthole solid. |
6. | Set the element size= to 3.0 and click mesh to create a tetramesh inside the Porthole. |
7. | Click return to close the panel. |
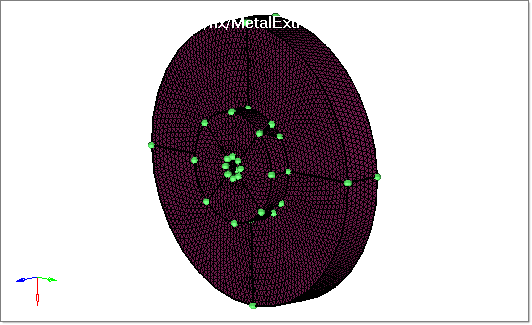
|
1. | Using the Model browser, right-click on the WeldChamber component and select Show. |
2. | Right-click on the WeldChamber3D component and make it the current component, and select Show to display it. |
3. | From the main menu, select tetramesh. |
4. | Select the volume tetra subpanel for meshing. |
5. | Click solids and select the WeldChamber solid. |
6. | Set the element size = field to 1.0 and click mesh to create a tetra mesh inside the WeldChamber. |
Note that the elements in two adjacent solids are connected at the shared surface.
7. | Click return to close the panel. |
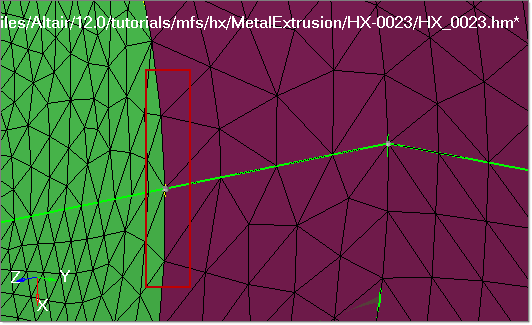
|
1. | Use the Model browser to show the display the Billet component. Make Billet3D the current component and show it. |
2. | From the main menu, select tetramesh. |
3. | Select the volume tetra subpanel. |
4. | Click solids and select the Billet solid. |
5. | Set the element size = field to 7.5. Click mesh to create a tetra mesh inside the billet. |
6. | Click return to close the panel. |
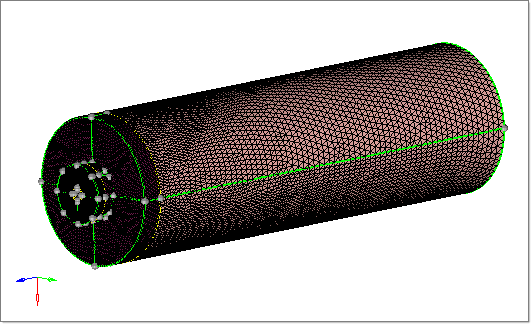
|
Use the Model browser to isolate the Profile3D component and set it as the current component.
1. | Right-click on Bearing3D and select Show. Click f to fit the model to the screen. |
2. | From the main menu, click faces to open the Faces panel. |
3. | Switch the toggle to elems. Click elems >> displayed. |
4. | Click find faces. The faces are placed into a component called ^faces, which is displayed in the Model browser. |
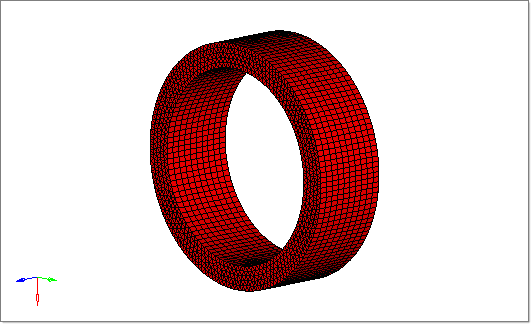
5. | Click return to close the panel. |
6. | In the Model Browser, isolate the ^faces component. |
7. | From the main menu, select the drag button. |
8. | Select the drag elems subpanel and select Z-axis for the drag direction. |
9. | Select an element on the model and click elems >> by face. The elements are selected. |
10. | Set the distance = field to 15, and set the on drag field to 15. |
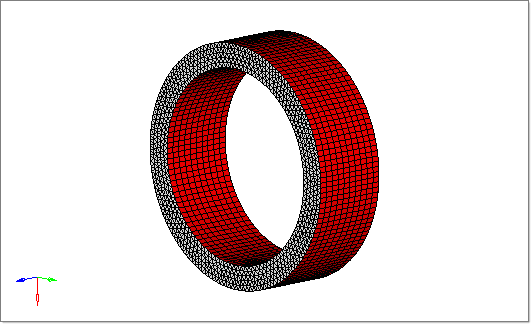
11. | Select exponential for the bias style and 1.0 for bias intensity. |
12. | Click elems >> displayed. The elements are selected. |
13. | Click drag+ to create elements in the profile region. |
14. | In the Model browser, right-click on Profile3D and select Show. Press f to fit the model in the screen. |
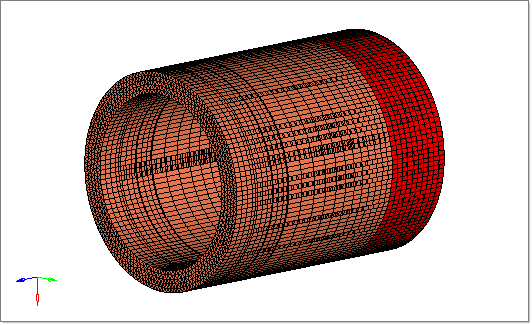
15. | Click File > Save As to save the model with 3D elements. |
|
After completing the mesh generation, use the Model Summary macro in the Utility menu to check the element quality.
1. | Click Model Summary on the Utility menu. This displays a window with model information. |
2. | Select the Element Statistics tab. This tab area lists all components with 3D elements with type of elements, number of elements and nodes in each component. |
3. | Click Show Element Quality. This calculates the aspect ratio, minimum, and maximum angles between adjacent edges of each element and checks if they meet the acceptability criteria listed in the table. |
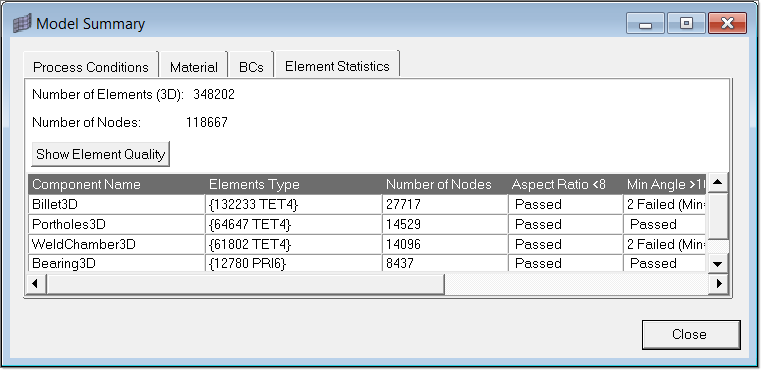
Element statics show that 3 WeldChamber3D elements failed the Min. angle criterion. However the slight variations (in this case, Min. angle of 8.1) in few elements are acceptable and the HyperXtrude solver will not pose any problem handling these elements. It is sometimes difficult to create the mesh (especially for Bearing3D and Profile3D) that satisfies all the quality criteria.
Here are some guidelines for checking mesh quality.
• | Max. Aspect ratio: TET4 < 8, PENTA6 <20, PYRAMID5 < 10; HEX8 <25. The way to understand the above requirements is, for example – recommended aspect ratio tet4 elements is that it should be less than 8. If this criteria is met then those element are of good quality. Hence by the test “Aspect Ratio < 8”, we check if the elements aspect ratio is less than 8. If yes, then it is considered a pass, if not the element is considered a failed element. HyperXtrude solver can accept reasonably large aspect ratio for PENTA6 and HEX8 elements. Most models use PENTA6 in the Bearing3D and Profile3D region, hence, the test “Aspect Ratio < 8” is quite stringent and should be taken with this guideline in mind. |
• | Min. value for “tet collapse” for elements in portholes and weld chamber is > 0.2 |
|
1. | From the File menu, click Save As. |
2. | Enter the file name in the field, being sure to give it a .hm extension. |
|
Return to Metal Extrusion Tutorials