Common Classification Parameters
Parameter | Label |
---|---|
Weld Type | Weld_Type |
Weld Category | Weld_Category_<Weld Type> |
Evaluation Distance Calculation Method | EvalDist Calculation Method |
- Weld_Type
- This parameter is automatically detected by HL-WC. The supported weld types are T, L, B, O, X and M welds. More information about weld types is available in The Weld Evaluation.
- Weld_Category
- Preset configurations for the classification parameters.
- EvalDist Calculation Method
- HL-WC allows two ways to calculate the evaluation distance using an automatic method and a manual method. The automatic method calculates the evaluation distance as a function of weld width and shell thickness of the components connected by the weld line. When using the manual method you can specify the distance in model units and HL-WC will use the value as is.
- Effective Weld Thickness (Ar)
- Ar (resulting weld thickness) is user-defined input. Based on this
parameter, there is a provision to reduce the stress values that are
captured from FE in specific sheets of the connection according to the
formula:
Stress (corrected) = Stress (current) * Ar / shell thickness
. This applies only to the stress normal to the weld and the shear stress. By default the value of Ar is set for the minimum shell thickness and then you can modify the value accordingly.Tip: Turn on the Enable Effective Weld Thickness option in Preferences to automatically set all weld lines to Yes in the Points Context. The option is disabled by default.Figure 1.
Direction Details
- Longitudinal Direction
- Direction parallel to the axis of the weld.
- Transverse Direction
- Direction perpendicular to the axis of the weld. There are two directions possible here, one towards the base material and other towards the web material.
Static Assessment
Use Static assessment to check for yielding/plasticity at weld locations. The Static evaluation process is carried out for all the evaluation locations based on the weld type. Von Mises stress component is used for this evaluation process. The maximum stress value across all the selected loadcases is compared against the material yield for any particular element.
Static Utilization = Max Von Mises / Material Yield Strength
General Stress Correction Based on Effective Weld Thickness
Where:
- - Stress value before correction (extraction from element at evaluation location)
- - Thickness of the shell at the evaluation location
- - Effective weld thickness
- - Intermittent factor, default = 1
- - Eccentricity, default = 0
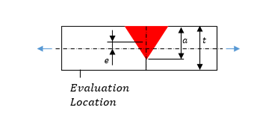
- Influence on Intermittent Factor ( )
- This factor is used to indicate the partiality of welds. This ratio describes the length of the weld that has actually been welded. Whenever the weld connection at any particular location is not continuous/complete, then you are suggested to modify/reduce this parameter to take into account the reduced weld material. (1 ≥ ≥ 0)
- Influence of Effective Weld Thickness ( )
- This parameter is used to consider the influence of welds which do not cover the same cross section area as indicated by the shell element in the respective evaluation location. It modifies the stress at the evaluation location based on the ratio to the shell thickness. ( > 0)
- Influence of Eccentricity ( )
- This parameter is used to consider the influence of welds which do not have the same cross section center as indicated by the shell element in the respective evaluation location. It modifies the stress at the evaluation location based on the induced bending stress. If > 0 the stress is increased. If < 0 the stress is reduced. If = 0 there is no influence.
- This option is activated in the General options section of the Points tool
and is available for all regulations.Figure 3.
- The default effective thickness calculated in the weld line browser under location details is based on the
following tables.
Table 1. Weld Locations Effective Thickness T-Weld 3, 4 0.7 0.7 * L-Weld 1, 2, 3, 4 0.7 0.7 * Butt-Weld 1, 2, 3, 4 1.0 1.0 * Overlap 3, 4 0.7 0.7 * M-Weld 3, 4, 7, 8 0.7 0.7 * X-Weld 3, 4, 5, 6, 9, 10 0.7 0.7 * Table 2. Weld Locations Effective Thickness T-Weld 1, 2, 5, 6 1.0 1.0 * Overlap 1, 2, 5, 6 1.0 1.0 * X-Weld 1, 2, 5, 6 1.0 1.0 * M-Weld 1, 2, 5, 6 1.0 1.0 * - The default calculated effective thickness can also be manually edited.