In this tutorial you will learn how to mesh the model using the solid map functionality in the Extrusion Wizard.
The model files for this tutorial are located in the file mfs-1.zip in the subdirectory \hx\MetalExtrusion\HX_0109. See Accessing Model Files.
To work on this tutorial, it is recommended that you copy this folder to your local hard drive where you store your HyperXtrude data, for example, “C:\Users\HyperXtrude\” on a Windows machine. This will enable you to edit and modify these files without affecting the original data. In addition, it is best to keep the data on a local disk attached to the machine to improve the I/O performance of the software.
Note: Solid map is valid only for solid profiles and not for hollow profiles.
1. | Select Start Menu > All Programs > Altair HyperWorks > Manufacturing Solutions > HyperXtrude to launch the HyperXtrude user interface. |
2. | The User Profiles dialog appears with Manufacturing Solutions as the default application. If it does not appear, you can access it from the menu bar by clicking Preferences > User Profiles. |
3. | Select HyperXtrude and Metal Extrusion. |
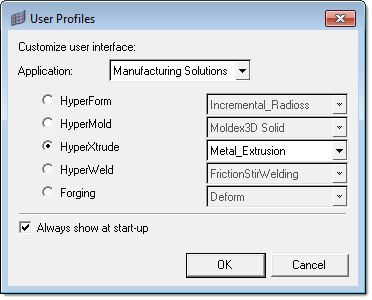
|
1. | Load the model HX_0109.hm. The model contains the solid geometry for the Billet, Pocket1, and Bearing components. |
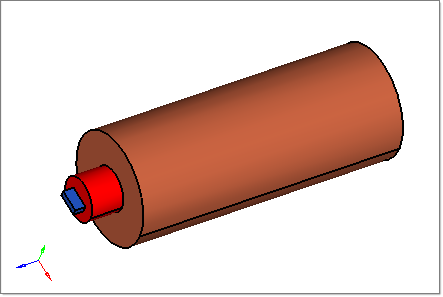
|
1. | On the Utility Menu, click Extrusion Wizard. Depending on how you loaded the model, the Project Browser may prompt you for additional action (see HX-0004 for details). |
2. | In the Extrusion Wizard, click Set Model Units. |
Note: Measure dimensions of the model by pressing F4 button on the key board to get an idea about the units of the model. In this model, the diameter of the container is about 10. This indicates that length unit is in inches. You will want to use Metric units for other parameters. So, select the Mixed unit system and set the units as shown in the figure below and click OK.
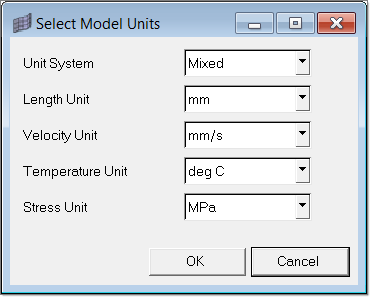
3. | Click Set Analysis Requirements in the Extrusion Wizard. The Process Data dialog opens. Observe all the default options and click Next to accept them. |

4. | In the Analysis Data page, click Yes on the last question. |
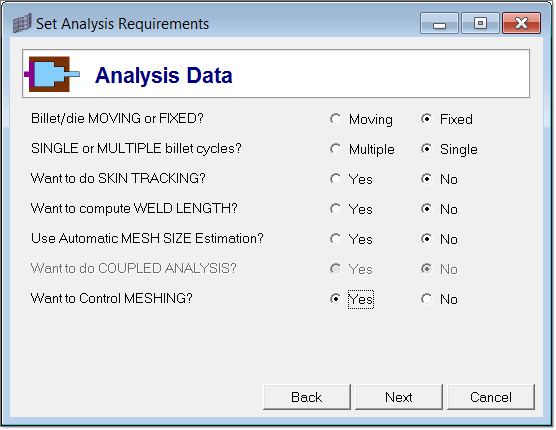
5. | Click Next to go to the Advanced Meshing Data page. |
6. | In the Advanced Meshing Data dialog, select one option from the following selections: |
• | To mesh the entire model using Solid Map, click Yes to the question "Mesh the Model by SOLIDMAP?" |
• | To mesh the Bearing component by Solid Map, click Yes for the question, "Mesh only the Bearing by SOLIDMAP?" |
• | To mesh the Billet component by Solid Map, click Yes for the question, "Mesh only the Billet by SOLIDMAP?" |
This exercise will mesh the entire model by Solid Map.
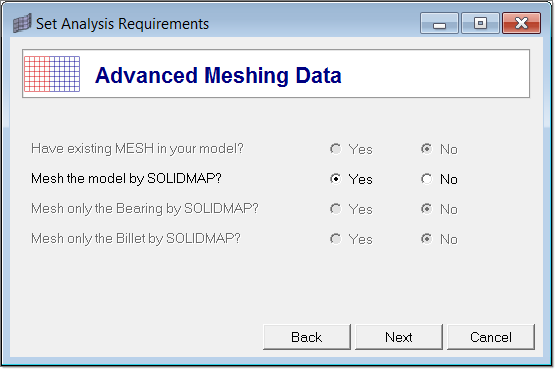
7. | Click Next to go to the Select Extrusion Components page. Check the box for the Pocket1 component and click OK. |
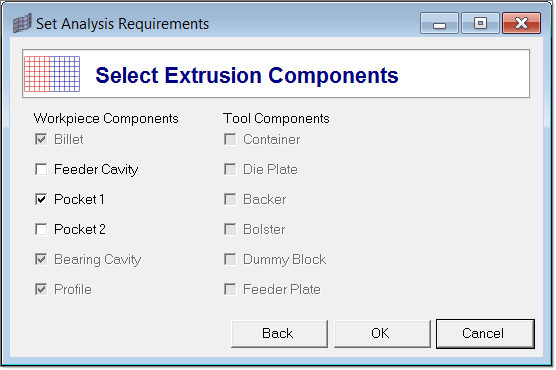
In the Extrusion Wizard, you will skip the Select Press Data step as this model does not contain the information.
|
1. | Click Select Material Data. |
2. | Expand Workpiece, then expand Aluminum_Alloys and expand 6000_Series. |
3. | Select AA6063 and click Add-> to add the material under Selected Materials. |
You do not need to assign a material in the Extrusion Wizard. The selected material will be assigned to the workpiece automatically.
4. | Click Close to close the Select and Assign Material from Database window. |
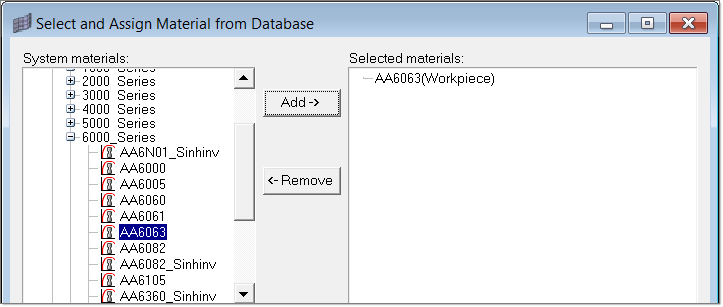
|
1. | In the Extrusion Wizard, click Generate Workpiece Mesh. Notice that the Extrusion Wizard already picked the components for Billet, Pocket1, and Bearing. |
2. | Input the size of the elements as shown below. |
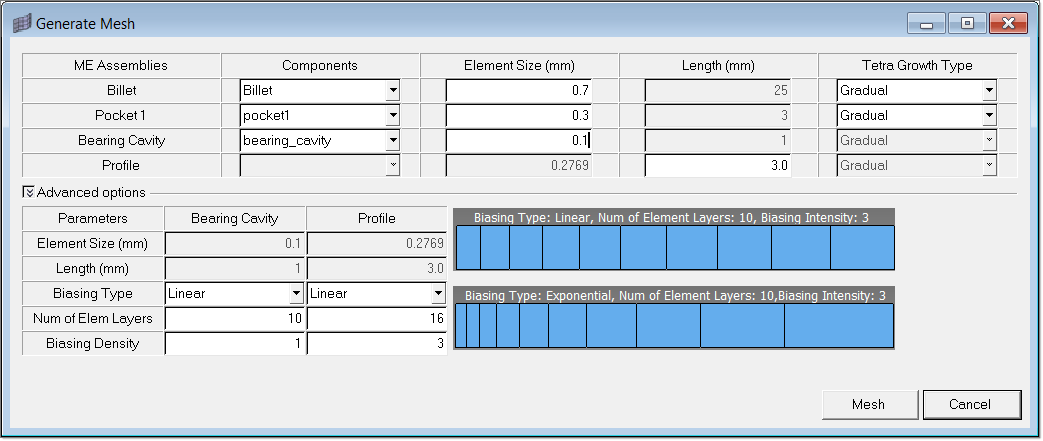
4. | After the mesh is created, click OK to close the dialog. |
In the Model Browser, notice that four more components are created - Bearing3D, Billet3D, Pocket13D, and Profile3D.
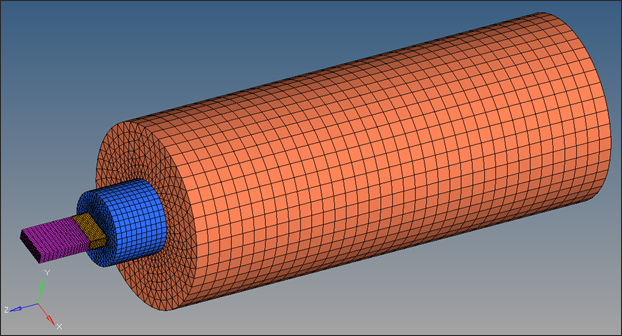
|
1. | Click Generate Workpiece BCs and accept the default conditions as shown in the Set Process Conditions window. |
2. | Click OK. This creates BC faces and associated load cards for all the 3D collectors. |
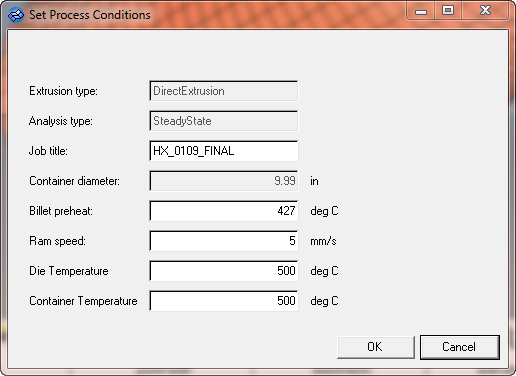
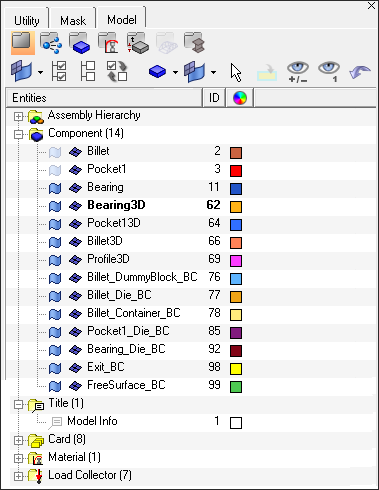
|
1. | On the Utility Menu, click on the Parameters macro to display the Define Altair HyperXtrude Analysis Parameters dialog. Observe all the parameters under different tabs. |
2. | Set the footer data in the User Commands tab to the following. This will help you invoke the solver in both interactive and batch mode. |
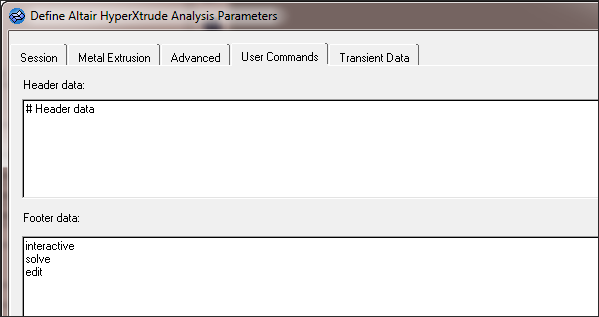
|
1. | In the Extrusion Wizard, click Save and Export the Model. |
2. | Browser to select the Project file name. Export the model with the following: |

3. | Click Export to generate HX_0109_FINAL.grf and HX_0109_FINAL.hx files. |
The .hx and .grf files can be passed to the HyperXtrude solver for solving analysis.
4. | To launch the solver interactively, set Launch solver: to Interactive and then export. |
Alternatively, you can set Launch solver: to No and submit the job on e-compute.
|
Return to Metal Extrusion Tutorials