Tutorial: Charge Weld Length
Learn how to compute Charge Weld Length by analyzing a model's post-processing information.
When extruding multiple billet cycles, the new billet material welds with material left in the pockets and feeder plate from previous extrusions. The quality of the material in this zone may not be acceptable and is usually sheared off. This sheared-off region, known as butt length, can be computed by performing billet interface tracking analysis in HyperXtrude. Billet interface tracking is performed as a transient analysis.
Load Model
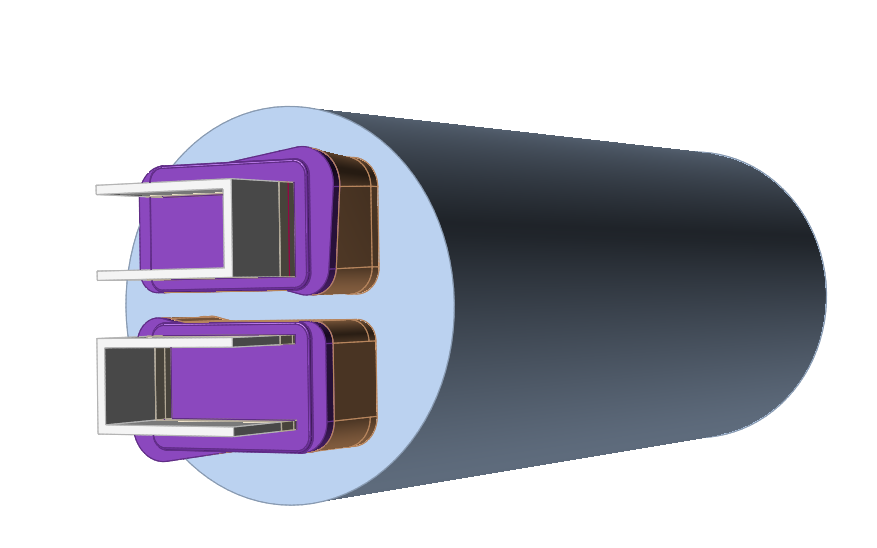
Select the Material
Specify Process Parameters and Simulate
Status after submitting the job |
![]() |
Status after meshing is completed |
![]() |
Status when job is running in the solver |
![]() |
Review the OUT File
The goal of post-processing is to understand the performance of the die. This is accomplished by studying the material flow and heat transfer in the model in HV. Before doing the detailed post-processing in HV, inspect the OUT file to get a quick overview of the results.
- Open the *.out file in a text editor.
- Inspect all data, applying the steps as outlined in the post-processing section.
Analyze the WLD File
View Simulation Results
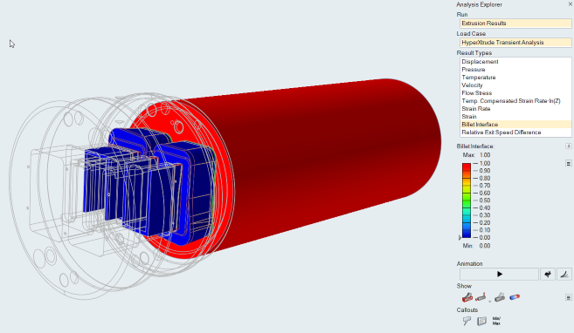
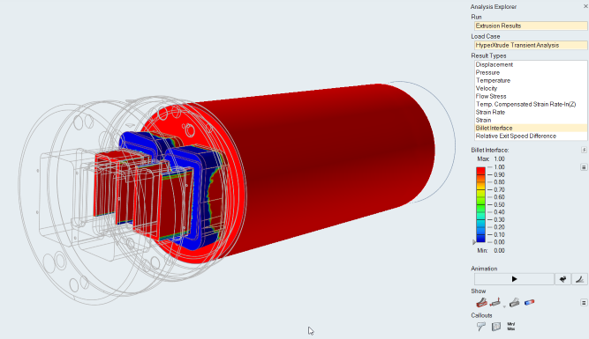
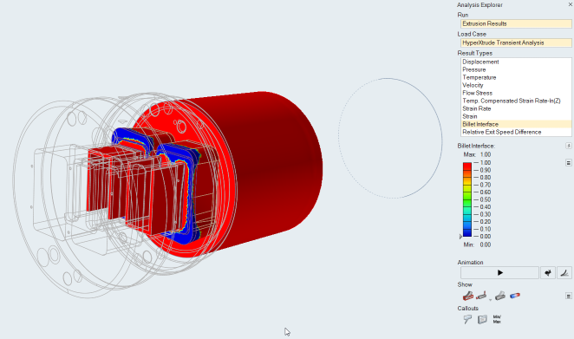
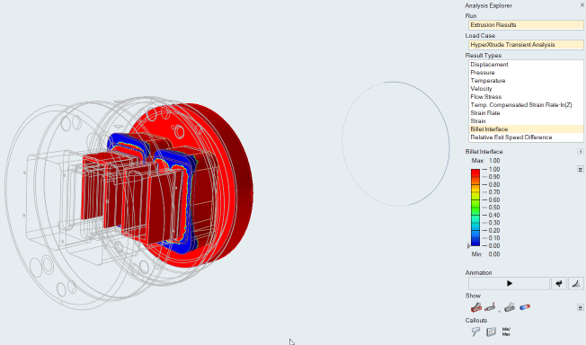