ACU-T: 5403 Piezoelectric Flow Energy Harvester: A Fluid-Structure Interaction
This tutorial provides the instructions for setting up, solving and viewing results for a simulation of a piezoelectric fluid harvester. In this simulation, a piezoelectric flow harvester is placed in a fluid flow channel. The harvester is attached to a cylinder mount which also acts as a bluff body causing vortices in the fluid flow. The interaction between the pressure fields generated by the vortices and the flow harvester structure is simulated in this tutorial. AcuSolve is used in conjunction with a structural solver to compute the structural displacement of the harvester using a direct-coupled fluid structure interaction (DC-FSI) approach. Arbitrary Lagrangian Eulerian (ALE) approach is used to compute the mesh deformation in the fluid domain as it interacts with the deforming structure.
- Set up a Direct Coupled FSI simulation (DC-FSI)
- AcuSolve/OptiStruct multiphysics coupling
- Setting up external code parameters to support coupling
- Assigning external code parameters to surfaces
- Analyze the problem
- Start AcuConsole and create a simulation database
- Set general problem parameters
- Set solution strategy parameters
- Import the geometry for the simulation.
- Create a volume group and apply volume parameters
- Create surface groups and apply surface parameters
- Set the appropriate boundary conditions for the coupling surfaces
- Set global and local meshing parameters
- Generate the mesh
- Run AcuSolve
- Monitor the solution with AcuProbe
- Post-process the nodal output with AcuFieldView
Prerequisites
You should have already run through the introductory tutorial, ACU-T: 2000 Turbulent Flow in a Mixing Elbow. Though not required, it is recommended that you have also run through ACU-T: 5400 Piezoelectric Flow Energy Harvester: A Fluid-Structure Interaction (P-FSI). This tutorial will demonstrate the same problem setup used in the P-FSI tutorial but with a DC-FSI approach. It is assumed that you have some familiarity with AcuConsole, AcuSolve and AcuFieldView. You will also need access to a licensed version of AcuSolve.
The coupled structural solver used for this tutorial is another HyperWorks product, OptiStruct. Thus, to follow this tutorial you will also need access to a licensed version of OptiStruct. The corresponding OptiStruct setup for this tutorial is available in the OptiStruct tutorial manual.
Prior to running through this tutorial, copy AcuConsole_tutorial_inputs.zip from <Altair_installation_directory>\hwcfdsolvers\acusolve\win64\model_files\tutorials\AcuSolve to a local directory. Extract fluid.x_t and slab_dcfsi.fem from AcuConsole_tutorial_inputs.zip. The file fluid.x_t stores the geometry information for the fluid portion of the model for this problem, and the file slab_dcfsi.fem is the OptiStruct input deck for this problem.
The color of objects shown in the modeling window in this tutorial and those displayed on your screen may differ. The default color scheme in AcuConsole is "random," in which colors are randomly assigned to groups as they are created. In addition, this tutorial was developed on Windows. If you are running this tutorial on a different operating system, you may notice a slight difference between the images displayed on your screen and the images shown in the tutorial.
Analyze the Problem
An important step in any CFD simulation is to examine the engineering problem at hand and determine the important parameters that need to be provided to AcuSolve. Parameters can be based on geometrical elements (such as inlets, outlets, or walls) and on flow conditions (such as fluid properties, velocity).
The schematics of the problem is shown in Figure 1. The CFD model consists of a cylindrical body and a cantilever beam. This cylindrical body generates vortex shedding. This vortex shedding creates a zone of alternating asymmetric pressure distribution on either side of the beam. Such an alternating pressure distribution exerts an oscillating force on the beam, creating a sustainable oscillating vibration in the beam.
The fluid solver does not require the solid body to be modeled. However, the structural solver will solve for the structural deformation using the fluid flow and pressure field which will be acting on the surface of the structure. The information required by the structural solver for structure displacement calculation will be passed on to it by the fluid solver. The structural solver on the other hand, will pass on the displacement information to the fluid solver. The fluid solver will then use this displacement information to calculate the flow field at the next time step, which will then be used by the structural solver to update the displacement information. This back and forth exchange of information between the fluid and structural solver will take place at each time step, and continue until one of the solvers signals the end of simulation. Figure 2 shows the arrangement of the beam with its various layers.
Fluid Structure Interaction
Fluid Structure Interaction is the interaction between a fluid flow and a deformable solid structure in contact with this flow. An FSI problem can be an external or an internal flow problem. The fluid flow can be external with the solid body immersed in the flow, for example, a windmill blade in open atmosphere. The fluid flow can also be internal with the solid body enclosing the flow, for example, fluid flow inside a deformable pipe. In both cases, the principle behind solving the problem remains the same. When a fluid flow encounters a structure, fluid pressure exerts a stress on the solid body that can lead to deformations in the structure. The magnitude of the deformation depends on the stiffness of the structure material and the magnitude of pressure force exerted by the fluid. The deformation in the structure shape then leads to altering of the flow characteristics in vicinity of the structure.
- Practical-FSI (P-FSI): The structure is reduced in the modal space and coupled to the fluid domain through interface nodes. The coupling between the solvers happens in a single pass itself. Structural behaviour is limited to be linear in a P-FSI simulation.
- Direct coupling (DC-FSI): The coupling is a co-simulation between the structural and the fluid solver, with each solver stepping through time simultaneously and iterating to equilibrium in each time step.
In case the deformations in the structure are large enough to alter the fluid flow significantly, the DC-FSI co-simulation approach should be used. With this approach, as the fluid flow and pressure fields affect the structural deformations, and the structural deformations affect the flow and pressure, the information about these effects is exchanged between the solvers in real time.
Given the difference in coupling methodology, it is likely that slightly different results will be observed when a same problem is solved using P-FSI and DC-FSI approaches. The choice of the approach that should be used shall depend on the problem and the available resources. As mentioned above, the P-FSI approach should be limited to the cases when displacements in the structure are small, and the structural behaviour can be approximated to be linear. For all other cases, DC-FSI should be preferred. However, DC-FSI simulations incur a higher computational resources cost. With this consideration, P-FSI simulation can also be used as a preliminary test simulation before a DC-FSI simulation is carried out.
FSI can be stable or oscillatory. In a stable FSI, the deformed shape of the structure will not change with time, unless the flow changes as well. In an oscillatory FSI, once the structure is deformed, it will try to return to its non-deformed state and then the whole deformation process repeats itself.
Mesh Motion Approaches in AcuSolve
- Arbitrary Lagrangian Eulerian (ALE)
- Interpolated Mesh Motion.
Arbitrary Lagrangian Eulerian (ALE)
ALE is an approach for mesh motion in which the computational nodes are moved arbitrarily with the aim of optimizing the element quality. An additional Partial Differential Equation (PDE) is solved to arrive at the appropriate mesh position. ALE is capable of handling complex arbitrary motions and is therefore the most general approach in simulating moving mesh problems. Generality comes with additional computational cost because of the extra PDE to be solved. For simpler motions like 1D or 2D motions faster approaches are available which include interpolated mesh motion, general specified motions, nodal boundary conditions based approaches.
Define the Simulation Parameters
Start AcuConsole and Create the Simulation Database
In this tutorial, you will begin by creating a database, populating the geometry-independent settings, loading the geometry, creating volume and surface groups, setting group parameters, adding geometry components to groups, and assigning mesh controls and boundary conditions to the groups. Next you will generate a mesh and run AcuSolve to solve for the number of time steps specified. Finally, you will visualize some characteristics of the results using AcuFieldView.
In the next steps you will start AcuConsole, and create the database for storage of the simulation settings.
Set General Simulation Parameters
In next steps you will set parameters that apply globally to the simulation. To make this simple, the basic settings applicable for any simulation can be filtered using the BAS filter in the Data Tree Manager. This filter enables display of only a small subset of the available items in the Data Tree and makes navigation of the entries easier.
Set Solution Strategy Parameters
Set Material Model Parameters
Import the Geometry and Define the Model
Import Geometry
Apply Volume Attributes
Volume groups are containers used for storing information about a volume region. This information includes solution and meshing parameters applied to the volume and the geometric regions that these settings are applied to.
When the geometry was imported into AcuConsole, all volumes were placed into the "default" volume container.
Since the model for this tutorial has only a single volume, it will be the only volume in the default volume group when the geometry is imported. Even when there is a single volume in the model, it is advisable to rename the volume for ease of identification in future. In the next steps you will rename the default volume group container, and set the material and other properties for it.
Create Surface Groups and Apply Basic Surface Parameters
Surface groups are containers used for storing information about a surface, including solution and meshing parameters, and the corresponding surface in the geometry that the parameters will apply to.
In the next steps you will define surface groups, assign the appropriate settings for the different characteristics of the problem and add surfaces to the group containers.
Set Surface Boundary Conditions
Set Parameters for the Inlet
Set Parameters for the z_neg and z_pos Surfaces
Set Parameters for the Slip Surface
Set Parameters for the Outlet Surface
Set Parameters for the Cylinder Surface
Set Parameters for the Beam Surface
Define Nodal Outputs
The nodal output command specifies the nodal output parameters, for instance, output frequency, number of saved states, etc.
Create Time History Output Points
Time History Output commands enables you to extract the nodal solution at any point within the domain. In this simulation, it would be interesting to observe the displacement at the tip of the cantilever beam.
Set the Initial Conditions
Create a Force Ramp Multiplier Function
The force acting on the beam, due to the flow, will be ramped gradually over the first few time steps. After these first few time steps, the complete force from the fluid will be transferred to the beam without any ramping. This will be achieved using a Multiplier Function. In the next few steps you will create a linear multiplier function which will later be assigned as a force multiplier function for load acting on the beam.
Set up the External Code Coupling
In the introduction it was discussed that the structural solver is responsible for calculating the displacement, and passes on the calculated displacements to AcuSolve. In the following steps, you will set up the connection between AcuSolve and the external code, which in this case is OptiStruct.
Assign Mesh Controls
Set Global Mesh Parameters
Global mesh attributes are the meshing parameters applied to the model as a whole without reference to a specific geometric volume, surface, edge, or point. Local mesh attributes are used to create mesh generation controls for specific geometry components of the model.
In the next steps you will set the global mesh attributes.
Set Surface Mesh Parameters
Surface mesh attributes are applied to a specific surface in the model. It is a type of local meshing parameter used to create targeted mesh controls for one or more specific surfaces.
Setting local mesh attributes, such as surface mesh attributes, is not mandatory. When a local mesh attribute is not found for a component, the global attributes are used as the mesh generation control for that component. If a local mesh attribute is present, it will take precedence over the global setting.
In the next steps you will set the surface meshing attributes.
Region of influence is a size control that allows you to control the size and growth rate of the surface and volume mesh surrounding a surface based on the distance from the surface.
Instead of repeating the above steps for the beam surface group, you can propagate the mesh attribute settings for cylinder surface group to beam surface group.
Define Mesh Extrusion
The present simulation is equivalent to a representation of a 2D cross section of the model. In AcuSolve, 2D models are simulated by having just one element across the faces of the cross section. Thus, when these faces are set up with an identical boundary condition, it coerces the corresponding nodes across the faces to have same results. In this problem, these faces are the negative and positive z-surfaces. This kind of mesh is achieved in AcuSolve with mesh extrusion process. In the following steps you will define the process of extrusion of the mesh between these surfaces.
- Expand the Model Data Tree item.
- Right-click on Mesh Extrusions and select New.
- Rename Mesh Extrusion 1 to z_extrusion.
- Right-click on z_extrusion and select Define.
-
In the Mesh Extrusion dialog, make the following
settings.
- Click OK to close the dialog.
Generate the Mesh
In the next steps you will generate the mesh that will be used when computing a solution for the problem.
Compute the Solution and Review the Results
Run OptiStruct
Run AcuSolve
In the next steps you will launch AcuSolve to compute the solution for this case.
Monitor the Solution with AcuProbe
AcuProbe can be used to monitor various variables over solution time.
View Results with AcuFieldView
- How to find the data readers in the File menu and open up the desired reader panel for data input.
- How to find the visualization panels either from the toolbar or the Visualization menu, so you can create and modify surfaces in AcuFieldView.
- How to move the data around the modeling window using mouse controls to translate, rotate and zoom in to the data.
This tutorial shows you how to work with steady state analysis data.
Start AcuFieldView

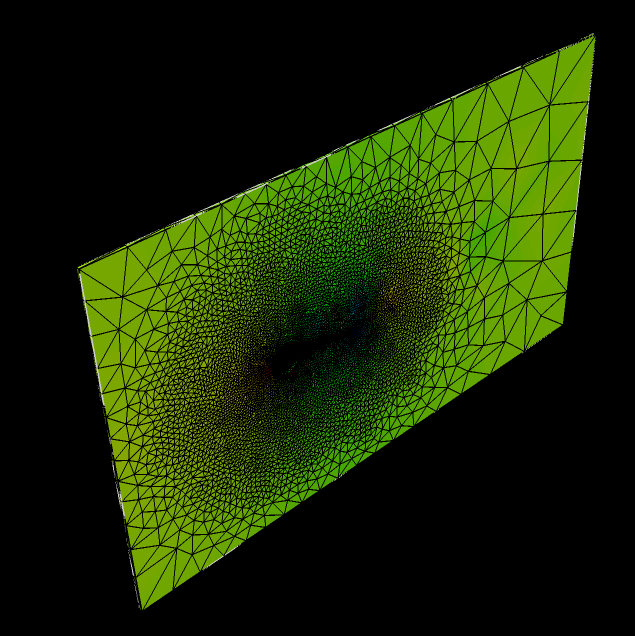
Set up AcuFieldView
View Beam Displacement Animation
If the Sweep Control in this dialog says Sweep instead of Build, the Flipbook Build Mode is not active. In Sweep mode, you will be able to create and visualize the animation but you will not be able to save it. To be able to save the animation, enable the Flipbook Build Mode.
Summary
In this AcuSolve tutorial, you successfully set up and solved an FSI problem using the Direct Coupling, or DC-FSI approach. DC-FSI approach is a co-simulation approach where both the structural and the fluid solvers run simultaneously, and exchange information at each time step of the simulation. The fluid solver passes the flow and pressure information to the structural solver, which are used to determine the displacements in the structure. The structural solver then passes the displacement information to the fluid solver, which then recalculates the flow and pressure field. Both the solvers thus update and exchange the results of the simulation to achieve the solution. You started the tutorial by creating a database in AcuConsole, importing and meshing the fluid portion geometry, and setting up the basic simulation parameters. Then you set up the structure which interacted with the flow such that its position was updated by the displacement data received from the structural solver at each time step. As a final step, you defined the parameters for setting up the connection between AcuSolve and the structural solver, and generated a solution with co-simulation. Results were post-processed in AcuFieldView, where you generated an animation of the beam’s displacement as it interacted with the fluid flow. New features that were introduced in this tutorial include: setting up a Direct-Coupled FSI simulation (DC-FSI), AcuSolve/OptiStruct multiphysics coupling, setting up external code parameters to support coupling, and assigning external code parameters to surfaces.